Posts Tagged ‘work’
How Factories Work
www.tvchoice.uk.com – How Factories Work – 56 mins, 2009 A set of 2 DVDs covering two essential elements of the manufacturing process methods of production and systems in manufacture. DVD 1: METHODS OF PRODUCTION Textbooks speak of three methods of production — job, batch and continuous flow. This film shows how the methods work in the real work. DVD EXTRA: Film shows how some of the most exclusive watches in the world are made – by hand. DVD 2: SYSTEMS IN A FACTORY This film looks at the key systems used in a factory. It focuses on two UK case studies: the Glaxo Smith Kline toothpaste factory and plastic injection moulding company, Time RPS. How do they compare? TVCHOICE has a range of over 200 educational films and film clips for Business Studies, Geography, History, Leisure and Tourism and many other subjects. USA FORMATS AVAILABLE. www.tvchoice.uk.com
Video Rating: 5 / 5
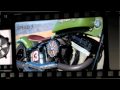
www.rolandsandsdesign.blogspot.com www.rolandsands.com Become a fan on facebook! VENTURI AIR CLEANERS When RSD set out to create an air cleaner, we wanted to make something that improved performance as well as the look of a bike. We ended up revolutionizing what an air cleaner can be in both function and aesthetics. The Venturi Air Cleaner features the best in filtration and flow from industry leader K&N. It is a proven high performance bolt-on part that drastically improves the looks of your machine. Our revolutionary backing plate promotes smooth air flow into the carb/throttle body while also providing hidden internal crank case breathers and our new tight seal oil separator insures a clean, leak free ride. Manufactured from Billet Aluminum in the USA, the Venturi is a jewel for the side of your bike. FEATURES: Seven Distinct Exposed Filter Designs Faceplates Designed To Match RSD Wheels Available in Multiple Finishes Built-In Crank Case Breathers High-Volume K&N Air Filter Included CNC-Machined From Billet Aluminium RSD Engraved Logo Stainless Steel Wire Mesh Screen Easy Bolt-On Installation Chrome Hardware Included *Not legal for sale or use on pollution controlled vehicles *Slotted breather bolts and Oil Tubes are included with all RSD aircleaners *All air cleaners can be used on Mikuni carbs with use of adapter – part number HS42/001-K (sold separately) VENTURI RAIN SOCK For those of you who do a ton of miles in the rain we recommend our new RSD Venturi Rain Sock …
Video Rating: 3 / 5
Q&A: Anyone else work in a factory?
Question by ArkyGirl: Anyone else work in a factory?
I have worked in a factory for 16 years (since I was 19). I run an injection molding machine that makes plastic parts. At the factory I work at we make knives- Ginsu knives, Pampered Chef knives, American Angler electric fillet knives. We also make vacuum cleaner parts for Kirby and Oreck. Just wondering if anyone else works in a factory.
Best answer:
Answer by Death byTaxes
It sure feels like a sweat shop sometimes, does that count?
Add your own answer in the comments!
what recycling ideas do you have for recyling in work place????
Question by poohnspice: what recycling ideas do you have for recyling in work place????
my work wants to get more in to recycling we need ideas . i work in a injection molding plastics manufactering plant. we already recycle pop cans and cardboard . and looking into pop bottles , we try to use both sides of copy paper when we can . when its permittable . i work in the assembly dept. and they just posted a paper wanting somebody to take charge, my boss thinks i would be the ideal person but not a leader but willing to hunt for suggesting . thanks for any ideas.
Best answer:
Answer by mrshunter_2002
collect bottles, at the end of the month turn them in, and have a office party
Give your answer to this question below!
injection moulding – will this work?
Question by cool: injection moulding – will this work?
I was thinking using a 7 bar compressor line to pressurise a 100cm dia vessel containing molten plastic(using 165deg hot oil jacket for eg :PP material) and using a valve arrangement to discharge the molten plastic inside a mould which is primirarily evacuated using a vacum pump driven by the compressed air itself .
Further addition of resin inside the chamber is acheived by forcing raw material using piston driven by air at higher pressure.
My calculations says there would be a 55Ton of force applied to the plastic inside the vessel. And since the mould is in vaccuum there is no possibility for any air locks.
Will this system work like a normal 50 Ton injection moulding machine ? (or) will it be impracticable a solution ?
Best answer:
Answer by Mr.Karachi
Well it is not clear the term valve, b/c valve type should be such no blockage taken place at that point. check out similar arrangement there should be needle valve is good.
It will work
Add your own answer in the comments!
Home made Injection Mould will not work for me
Hi all, I wanted to see if I could injection mould a cheap little plastic dust pan at home. I was successful in making a concrete mold by using a taped plastic prototype and clay. Turns out that the Smooth-on.com product smooth cast 45 does form the cast, but, it takes way to long to make each piece enough to make any money selling the final pieces. With that in mind, I figured I would try to make a home made injection mould by welding soft iron sheets together. I use the Harbor Frieght sheet metal shears, as well as a chop saw, and they all worked well enough for me to cut the proper sized pieces. The only problem is that the Low Density Poly Ethelyne ( LDPE ) is Way too viscous to flow into any metal form that I make. You will see from the video that even though the melting point of LDPE is 248 F, it does not easily flow into the mould without high presure. If anyone has any suggestion, please feel free to let me know how I can make an injection mold piece at my house.
Video Rating: 4 / 5
Is it dangerous to work in a plastic factory and breathe in the air expelled by the machines? AOKI?
Question by gib g: Is it dangerous to work in a plastic factory and breathe in the air expelled by the machines? AOKI?
The factory has extrusion blow molding, injection, and stretch blow molding machines such as AOKI DIRECT HEATCON Stretch blow molding machines. Is it ok to breathe in the air expelled by these machines and are there any real dangers to working in a plastic factory overall? By the way the plant is called BERRY PLASTICS
Best answer:
Answer by Jules
Yes, it is VERY dangerous. I would be very careful if I was you
Know better? Leave your own answer in the comments!
How Does an Injection Moulding Machine Work?
How Does an Injection Moulding Machine Work?
An injection moulding machine is a complex piece of machinery that creates one solid piece by injecting molten materials through a reciprocating screw system into a mould. This machine is made of many components; it is primarily consisted of a hopper, a barrel containing a reciprocating screw, temperature control devices, a clamping unit and the injection mould itself.
The process begins with the creation of a mould. The mould is created by the Toolmakers from the specifications given to them from the designer or engineer via a 3D computer-generated model. The mould is carefully constructed to allow the two halves of the mould — the mould cavity and the mould core — to separate along the parting line. This will allow easy ejection from the injection moulding machine when the part has cooled. If the mould is designed incorrectly the part may catch on the mould, resulting in possible damage.
The specifications and components of the machine must be carefully set up before the process of injection moulding can begin. Temperatures and pressures will be programmed according to the size and shape of the mould and the material that the part is to be made from. Once the machine is set, the cycle will begin and the machine can be left unattended to work its magic.
This is how it works:
Raw material and colour is fed into the barrel of the machine via the hopper. In the barrel the raw materials are subjected to pressure and temperature until they are melted and malleable. The reciprocating screw inside the barrel will turn, injecting a precise amount of the now molten plastic into the injection mould at a set and controlled temperature, pressure and speed. Once the mould is filled with the molten plastic the injection process will shut off. The part is then allowed to cool until it is ready to be taken from the mould. This can take some time depending on the materials, wall thickness, overall size and shape of the part being manufactured. When cool, the mould will open automatically. The mould is inbuilt with an ejecting mechanism which ejects the part in preparation for a new cycle. If a portion of the finished part is still caught in the mould at this point the mould will reopen until the part has been completely ejected. When the part is clear of the machine, the hopper will release more raw material and colour into the barrel and a new cycle will begin. The autonomous nature of the injection moulding machine means it can be left unattended once programmed, and may run continuously throughout day and night.
The basic concept of the plastic moulding machine has been around for over seventy years. Since then the original idea — injecting molten plastic into a mould — has evolved dramatically into an efficient, elegant and versatile tool for creating everyday items.
Dienamics is the only company in Brisbane to offer the complete service of Industrial Design, Toolmaking and Manufacturing. We specialise in the custom moulding of components using engineering thermoplastic resins. For more information, visit <a rel=”nofollow” onclick=”javascript:pageTracker._trackPageview(‘/outgoing/article_exit_link’);” href=”http://www.dienamics.com.au”>Injection Moulding</a>.
Related Plastic Injection Articles
What Is Injection Plastic Mould And How Does It Work?
What Is Injection Plastic Mould And How Does It Work?
Injection plastic mould is a way of creating multiple parts that are the same shape. For example, if you have a manufacturing company and you need to create a large volume of plastic parts that are the same shape and size, then you would use plastic injection plastic mould machines to speed up your production line. The great thing about it is that it’s cost effective and it also requires little supervision from staff.
Injection rapid prototype works in a few stages. Firstly, the plastic is melted and pushed into a rapid prototype. The mould is then squeezed together to form the shape of the piece required. Next the machine will cool the mould (usually using water) and you are then left with a perfectly formed piece of plastic ready for the next stage in your production line.
Most of the time, people use injection plastic mould to make things faster and to make sure that things are very accurate. The machines that are used are all computerised and this means that they run like clockwork and are very accurate. They are ideal for creating the same product over and over again in a hurry.
Car manufacturers use these machines a lot – so for example, the lid of a radiator bottle in a car will be created using this. There are hundreds of cars made every year and therefore this sort of process is required to ensure speed and accuracy.
Hand making plastic products like this would be a real nightmare and although sometimes this is required, injection plastic mold is simply used when speed is of the essence. It’s also very cost effective because the only costs are the initial purchase, the plastic mold and of course water to cool the moulds when needed.
This makes it a very popular option for businesses who need to make things like this. Most major manufacturers use this service and there are a lot of options available on today’s market. You should have no problems finding something that’s suitable for your needs.
www.longxiang-ltd.com are a professional manufacturing company for precise plastic mould, plastic molding and rapid prototypes by CNC etc. in China. welcome to order.
Innovative, cost-effective blow molding and injection molding machines and custom plastic processing machinery at Wilmington Machinery. Make your own plastic pallets, bottles, containers and other parts.
Video Rating: 0 / 5
Find More Plastic Injection Articles
How do Injection Moulds Work?
How do Injection Moulds Work?
An injection mould is the key to creating a successful one-piece finished plastic or metal component. Melted material is forced from the injection moulding machine into the mould (which is usually cool) where it sets. The result is a solid piece of the material which may be a component to, or the whole of, a finished product.
The mould is created by skilled technicians called Toolmakers who usually shape the mould according to the specifications of a 3D computer-generated model, which in turn has been created from the specifications of the product designer.
Injection moulds, or dies, have two halves that, when combined, create a whole that contains a hollow. It is into this hollow that the hot plastic or metal is injected and cooled, resulting in an exact physical copy of the 3D model. The two halves are commonly referred to as the mould core and mould cavity. The mould core corresponds to the inside surface area of the finished product, whereas the mould cavity corresponds to the outside surface area. The line which divides the two halves of the mould is called the parting line. This must be carefully chosen and designed around so as to allow the mould to separate properly. Serious damage can be caused if the mould contains an undercut or overcut, caused by a protruding portion of the mould which snags on the mould core or mould cavity respectively. There are countless ways to work around these design limitations.
An injection mould may seem a simple tool, but the complexity of the modern injection mould goes way beyond putting two hollows together to create a whole. Injection moulds are highly advanced pieces of technology. Once programmed, they are able to run autonomously day in and day out without any assistance. Moulds are set up with their own feeding system for the raw plastic and temperature control system to measure with precision exactly how the material is maintained — heated for injection and cooled for setting. They contain ejector systems to release the parts once they are complete. All of these systems reduce the need for personnel and can be left to run overnight, reducing costs dramatically.
As with any product, the quality of the mould and materials used dictates the quality and consistency of the parts that they will produce. Sundry plastic items like free coat hangers from department stores or DVD cases will be relatively cheaply produced as they will be made by the thousands, the quality of materials will not be considered a worthwhile investment and the variance in consistency will be negligible. For more consumer-attractive products, such as the dashboard for a limited edition car, the manufacturers will be certain that the plastic is of a high quality to ensure consistency and quality in their product.
Plastic injections moulds are based on a basic idea that has been refined to an art. Adaptable and so often used, the products created in injections moulds are all around us.
Dienamics is the only company in Brisbane to offer the complete service of Industrial Design, Toolmaking and Manufacturing. We specialise in the custom moulding of components using engineering thermoplastic resins. For more information, visit <a rel=”nofollow” onclick=”javascript:pageTracker._trackPageview(‘/outgoing/article_exit_link’);” href=”http://www.dienamics.com.au”>Injection Moulding</a>.
How does soft plastic injection molds work?
Question by trout_tapout: How does soft plastic injection molds work?
Best answer:
Answer by MJ23_4life
I hope this helps:
http://pslc.ws/macrog/kidsmac/molding.htm
Know better? Leave your own answer in the comments!