Posts Tagged ‘Technologies’
Khatod Coating Technologies
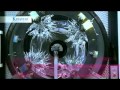
Khatod Optoelectronic Srl – High Tecnology, Best Quality Service: This Is Our Must Khatod is the unique company on the international scene that specifies and develops the entire product process 100% in-house. Since 1985, Khatod has held all of its operations in its headquarter (Milano, Italy) a full optical service – from project to object – encompassing optical and mechanical designs, mould fabrication, injection moulding, test and inspection, as well as the time to market, are under our full control. Our quality starts from close collaboration with selected suppliers, world leaders in plastic materials, control instruments, and machines for polymers transformation process. Most of the technologies used to produce our millions of parts per month, are created by our team of engineers who develop our new, technically unique products as well as creating the necessary tooling and equipment to manufacture them. Today, we are proud to announce that, since the beginning of 2012 Khatod has equipped its Production Department with the most advanced vacuum treatment plant based on the latest cutting-edge VACUUM COATING TECHNOLOGIES, specific for coating our Optical Reflector Systems for LED applications. Always in the same spirit: 100% in-house, under our full control, from project to object, our aim is to deliver our customers the highest quality level. The realization of our vacuum treatment plant has been carried out in collaboration with the R&D of one of the most important …
3D Printing – Polyjet – Additive Technologies (Rapid Prototyping)
This is Episode 1 of a series of video blogs on Additive Technologies (also known as Rapid Prototyping). Today we’re looking at the Multi-Material Polyjet machines which can mix both rigid and soft materials together on the fly to grow parts that simulate over-molding and other complex applications. This process is great for small to medium sized parts (it’s not always cost effective for large parts) and is often used for a variety of prototyping applications (the material is not usually suited for end-use applications), creating a direct tool for a silicone mold, and investment casting.
Video Rating: 4 / 5