Posts Tagged ‘Super’
NEW – Funky Golf Grips – Super Stiki. By Funkd Golf
The manufacturing method for the Funky Golf Grips™ is different from the rubber grips. We use a process called “injection moulding.” The synthetic thermoplastic rubber is injecting into a die cast at high temperatures. This produces a seamless golf grip with very little weight variation (error within ± 0.5g). The material makes our Funky Golf Grips™ feel different than our other rubber grips. The golf club grips are soft, flexible, water proof, sweat proof and crack proof. The grip texture has been computer designed to be non-slip and deep cut. Funky Golf Grips™ 3 have a hardened coloured end cap for superior durability.
nexflowair.com The Nex Flow™ Model 45002 — high force adjustable air jet amplifies air flow and creates a strong laminar flow of output air to be able to push injected molded material down and away from the mold after the molding process allowing for faster cycles times. Utilizing very little compressed air the output air is amplified almost 25 times when it hits the target part with a strong laminar force to “push” the parts down and away from the mold. (by Nex Flow™ Air Products Corp.)
Heidi’s boobs & the Retarded Super Bowl
Some bowling team in New Orleans wins a game, Sarah Palin gets mad at Rahm Emmanuel for calling people retarded, Jay Leno is apparently an evil manipulative puppet master from hell and Heidi Montag should get more surgeries until she is 100% plastic
Video Rating: 4 / 5
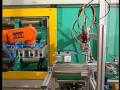
At one time, the injection molding machines for polyurethane sheathing, used by Gross + Froelich to manufacture its so-called soft wheels for furniture casters, were loaded with polyamide cores manually. Subsequently the handling was carried out by linear units. Later, the user wanted to introduce a new product and to increase capacity, and therefore began looking for a more efficient automation solution. This would require short cycle times, in order to prevent delays in the manufacturing process and thus the associated rejects. This is because the injection molds have to be loaded with wheel cores as quickly as possible. If they remain open too long, there is a risk that part of the polyurethane will cool and have to be removed from the mold manually.
Video Rating: 0 / 5