Posts Tagged ‘stress’
Stress Engineering – PET Bottle Stretch-Blow Molding Simulation
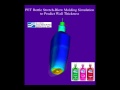
Preform design, blow-molding process conditions, bottle wall thickness distribution and ultimately bottle performance (such as, topload capacity and squeeze/dispensing characteristics) can be optimized using this blow molding simulation coupled with bottle structural analysis. The goal is to minimize the bottle weight and maximize the bottle performance for sustainability. For more information, please visit us at www.stress.com. Contacts us at youtube@stress.com with any questions.
Static Stress, Linear Dynamics, and Heat Transfer Overview – Autodesk Simulation
Want more information after viewing this video? Be sure to visit www.autodesk.com and www.SIMSquad.com. Autodesk® Simulation software, part of the Autodesk® solution for Digital Prototyping, provides a range of mechanical simulation tools to help designers, engineers, and analysts make decisions earlier in the engineering design process. With these tools, you can predict the real‐world performance of your product, helping to save the time and money required to build multiple physical prototypes. Autodesk® Simulation Mechanical and Autodesk® Simulation Multiphysics software includes tools for static stress and linear dynamic simulations—helping you study stress, strain, displacement, shear, and axial forces resulting from structural loading—including forces, moments, pressures, gravity, and displacements. Autodesk® Simulation software also helps you determine a part’s natural frequencies and mode shapes in order to avoid frequencies that are disruptive or harmful to your design. In addition, it helps you avoid structural failure by determining the amount of load that would cause a structure to buckle—letting you review the predicted buckling shape so you can then add supports and stiffeners to your design. Autodesk® Simulation software includes support for steady-state and transient heat transfer simulations—helping to predict changes in a product’s temperature profile in order to reveal potential failure. Study linear and nonlinear thermal effects by considering …
Video Rating: 5 / 5
How to limit or reduce residual stress in injection moulding process?
Question by Zed: How to limit or reduce residual stress in injection moulding process?
Just try to limit the birefringence of polycarbonate that occured during the moulding process.
The main cause is the residual stress in the course of moulding, So how do I reduce this? Any idea?
Best answer:
Answer by a.gash
Thixomolded parts are said to exhibit mechanical properties equivalent to or better than die casting , with half the porosity , and tighter part tolerances leading to reduced shrinkage , reduced residual stress and less component distortion. No foundry is required , there is no molten metal handling with its associated losses from flux , sludge or dross , and the process eliminates the use of sulphur hexafluoride , a suspected greenhouse gas which is used in magnesium foundries .
http://www.polymer-age.co.uk/archive2.htm
These residual stresses are mainly frozen in thermal stresses due to inhomogeneous cooling , when surface layers stiffen sooner than the core region as in free quenching. Additional factors in injection molding are the effects of melt pressure history and mechanical restraints of the mold .
http://www.mmpc.mcgill.ca/page4.html
What do you think? Answer below!