Posts Tagged ‘plastic’
Q&A: how can we use the rubber injection press machine for plastic injection?
Question by mohamed: how can we use the rubber injection press machine for plastic injection?
we have a rubber injection press machine we like to use it -with modification- to plastic production as plastic injection press
Best answer:
Answer by redbeardthegiant
Ask the manufacturer. They would probably love to sell you whatever bits you need for the conversion.
Give your answer to this question below!
Are there companies that do plastic injection molding with recycled plastic?
Question by mtgentry81: Are there companies that do plastic injection molding with recycled plastic?
And is it much more expensive than the normal way?
Best answer:
Answer by kerry k
Yes, and that depends on what the plastic is.
Add your own answer in the comments!
2004 FORTUNE VS100 PLASTIC INJECTION MOLDING MACHINE
FORTUNE 110-TON PLASTIC INJECTION MOLDING MACHINE, MODEL VS100, 6.1 OZ (173 GRAMS), 40 MM (1.57″) GP SCREW, MAN. IN 10/2004, INSTALLED DECEMBER 2004, V8000 SEMI-CLOSED LOOP CONTROLLER, 16.14″ x 16.14″ (410 MM x 410 MM) TBS, 22.83″ x 22.83″ (580 MM x 580 MM) PLATENS, 31.1″ (790 MM) MAX. DAYLIGHT, 25 HP MOTOR WIRED AT 480 VOLTS, DIM: 168″L x 56″W x 79″ H, WEIGHT: 10800 LBS., INCLUDES OPTIONS OF SINGLE CORE PULL, SINGLE AIR BLOW, MODULAR CHECK VALVE TO LOCK CARRIAGE CYLINDER, 3-PHASE ACCESSORY SOCKET, LINK TO EXTERNAL PRINTER, AUTO CLAMP FORCE SET-UP, MOLD WATER TUBE MANIFOLD, SCREW RPM DISPLAY, SPI ROBOT INTERFACE, MOTION/NO MOTION, POWER TIME 9827 HOURS, 1534.5 AUTO WORK TIME, AND 443463 CYCLES ON 03/14/2008, RAN MOSTLY PP, USD 841 WHEN PURCHASED NEW IN 2004, WEBSITE PHOTOGRAPHS www.acmeplasticfl.com MACHINE SPECIFICATIONS www.acmeplasticfl.com
Plastic injection moulding using robot seperating sprue and LH & RH impressions, lights out
Video Rating: 0 / 5
Analysis US Injection Molded Plastic Industry
Analysis US Injection Molded Plastic Industry
US injection molded plastic demand will approach 16 billion pounds in 2010 based on diverse applications and cost efficiency, and rebounding markets. Polypropylene will present the best opportunities with fastest growth anticipated in medical, packaging, and electrical and electronic markets. Thermoplastic resins will remain dominant.
This study analyzes the 13.9 billion pound US injection molded plastic industry. It presents historical data for 1995, 2000 and 2005 and forecasts to 2010 and 2015 by resin (e.g., polypropylene, polyethylene, polystyrene, ABS/SAN, PVC, nylon); and by market (e.g., packaging, consumer, motor vehicles, electrical and electronic, medical).
The study also considers market environment factors, details industry structure, evaluates company market share and profiles 42 major producers including Collins & Aikman, Delphi Automotive Plastics, Lear, Berry Plastics, Visteon, and Plastech Engineered Products.
Injection molded plastics demand in the US is projected to grow 2.8 percent annually to almost 16 billion pounds in 2010, valued at .7 billion (resin content only). Resins will account for 40 percent of total injection molded product costs of .8 billion. Advances will reflect injection molding’s diverse applications and cost efficiency, as well as rebounding markets. Resin and machinery improvements will also expand applications by enhancing product performance, quality and throughput. Thermoplastic resins will remain dominant due to processing, design and recycling advantages over thermosets. These and other trends are presented in Injection Molded Plastics. For example <a rel=”nofollow” onclick=”javascript:pageTracker._trackPageview(‘/outgoing/article_exit_link’);” href=”http://www.cikmold.com”> casting mould,mold making,plastic injection mold </a> etc.
Polypropylene, high density polyethylene and polystyrene together accounted for 63 percent of all Injection molded plastics demand in 2005. Injection molded polypropylene demand is forecast to rise 3.6 percent annually based on the resin’s low cost, good performance and improved performance characteristics such as clarity and melt strength. Best opportunities are anticipated in packaging uses such as caps and closures, and housewares and personal care products. Demand for injection molded high density polyethylene will be fueled by industrial packaging opportunities such as shipping pails, and totes and crates.
Injection molded polystyrene demand will increase slowly due to competitive pressures from lower cost resins such as polypropylene and high density polyethylene. Nevertheless, polystyrene remains one of the best materials for injection molding, with good growth anticipated in electrical and electronic components, and consumer products. Best growth is expected for injection molded thermoplastic polyester and polycarbonate.
Measurements and analyses of the energy used in primary processes, ancillary services, and the building envelope were included in the assessments. Using the resulting data, IAC staff were able to identify opportunities for energy savings, waste-reduction measures, and productivity improvements for each plant. IAC faculty and students captured these opportunities in a set of recommendations made to the individual companies. A broad sampling of the recommendations is included in 11 case studies that are intended to help other companies identify similar opportunities for savings in their own manufacturing operations.
Packaging and consumer markets together accounted for 64 percent of total injection molded plastic demand in 2005. Packaging markets will be driven by opportunities in caps and closures, as well as industrial shipping pails, and totes and crates. Consumer market growth will reflect needs for inexpensive, convenient, lightweight and unbreakable housewares and personal care products such as storage containers and razors. Threatening further advances will be saturation in many areas such as appliances and toys and recreational products, as well as continued import growth from low cost offshore producers such as China.
Steven ZHAO is a MBA and CTO of BPWork.com Info-Tech Co., Ltd,- A professional offshore outsourcing services provider company in China & Australia specializing in Data entry and processing, Software development, Software testing, Database support, Website design, Software localization, Multimedia localization and BPO.%d%ahttp://www.bpwork.com%d%a%d%a
Related Plastic Injection Articles
What temperature should the nozzle of a plastic injection machine be if you were to use polypropylene?
Question by Leo: What temperature should the nozzle of a plastic injection machine be if you were to use polypropylene?
Where would one find this information?
Best answer:
Answer by Yoho
The company you bought your material from
http://www.ides.com/generics/PP/PP_processing_information.htm
Add your own answer in the comments!
Q&A: I need a good website to study plastic injection molding.?
Question by williestyle1111: I need a good website to study plastic injection molding.?
I’ve just been promoted to supervisor at the factory I work at and I need to learn more. I’m getting some on the job training but I want to find a good website that I can study from at home to try to get ahead. I want to learn more about things like the press parts, trouble shooting, repairs, defects, ect. Any help would be welcome. Thanks.
Best answer:
Answer by William B
try ask .com how its made .com library,
library of congress.com
What do you think? Answer below!
do you need a cooling tower to cool the molten plastic from the plastic injection molding machine?
Question by charLee: do you need a cooling tower to cool the molten plastic from the plastic injection molding machine?
how does the molten plastic inside the mold cool? does is cool all by itself? please help…i am really confused…do you know how many kw cooling towers consume per hour?
Best answer:
Answer by Aydin
The most economic answer is not. I mean you don’t need any cooling tower but it depends on the situation and amount of plastic which you are injected in mold.
As I saw different cases for commen mold they don’t use any cooling equipment and plastic cools down itself.
Know better? Leave your own answer in the comments!
Plastic injection moulding with robot lights out
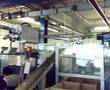
Plastic injection moulding using robot seperating sprue and LH & RH impressions, lights out
Video Rating: 5 / 5
custom plastic injection molding
custom plastic injection molding
Injection mildew design is an element of the fast-paced world of injection molding. When as a mildew designer, you must be able to think about new techniques of making things, and be flexible and ready to learn new technologies.It might look easy due to the powerful CAD programs, but in actual fact these programs are merely the instruments to help prepare your design. In the field of injection mold design you regularly must develop new and original techniques of plastic molding.
what is a normal day like for a mold designer? Mold designers and mildew makers work closely together. This is patently for the explanation the mildew maker will be using the design to build the mildew. Mold makers and mould designers have a really similar daily schedule, though mould makers seem to work longer hours.Generally, a plastic mould designer works all day at his computer using some really sophisticated mildew design platforms. There are a lot of top-end design programs,eg SolidWorks, MasterCam, AutoCad, Unigraphics, and lots more. These applications enable the designer to rapidly look after details that previously took days of hand drawing.
Very often the mould designer will be required to communicate with the various mold makers, CNC programmers, WEDM operators, etc.. The mould designer must be ready and able to communicate, if he is to achieve success. Very often injection mold designers work less hours than their mould maker opposite numbers. It’s also common for mould designers have a shop background and help out in the mould making shop also. This is especially true if there’s a deceleration in design and plenty of work in the store.
How to turn an injection mold designer? Fundamentally, there are 2 trails in the United States. One path is to work as a mould maker and later move into the design area. The other trail is to attend a college or university to become qualified. Both approaching are quite common.Since so many plastic molding designers come from a mildew making background, they are able to bring practical experience to the job. This is especially useful to provide a realistic approaching to mold design. There’s nothing quite like practical experience!
If you are looking into purchasing Custom Injection Molding or would like a Injection Mold Design, then the above site is the place to visit.
because we live and operate in a world economy, it isn’t even a prerequisite to work in the same country as the mould maker, though it is simpler if you do. There are many mold designers who independent out of their own small office and are quite happy doing so. This is a workable alternative for the right person.Conclusion Injection mildew design is a highly respected occupation with really low unemployment and good pay. Most mildew designers have secure jobs that provide a cosy living with a minimum of occupational dangers, compared to other roles. It’s also very possible to work as a freelancing mold designer and have substantial freedom of trend.
.
Hello Everyone,
Happy to join this great community. Looking forward to contribute and learn from you all.
Related Plastic Injection Articles
Plastic Injection Molding Machine
Plastic Injection Molding Machine
Video Rating: 4 / 5
visit www.cnmoulding .com for details first time test for baby toy that learn walking.
Video Rating: 4 / 5