Posts Tagged ‘plastic’
plastic injection molding mould maker china
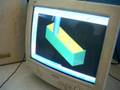
we have high capacity to design and make high quality mould and die, and produce part for our customer we are waiting for you come and cooperate. visit www.cnmoulding.com for details

www.HQCInc.com , located near Chicago and known as the plastic caps and closures specialists, HQC Inc. is a Chicago market Plastic Injection Molding company. Our Chicago market – Midwest based plastic caps and closures, plastic caps, plastic bottle caps and plastic closures facility is tops…
Video Rating: 0 / 5
Injection Molding-How Plastic is Molded
Injection Molding-How Plastic is Molded
Plastic has, quite literally, become the cornerstone of our society. We make so many things from plastic that it is hard to imagine what our lives would be like if it was never invented. With so many of our everyday products being made of plastic, it is easy to understand why plastic injection molding is such a huge industry.
Approximately 30% of all plastic products are produced using an injection molding process. Of this 30%, a large amount of these products are produced by using custom injection molding technology. Six steps are involved in the injection molding process, after the prototype has been made and approved.
The first step to the injection molding process is the clamping of the mold. This clamping unit is one of three standard parts of the injection machine. They are the mold, the clamping unit and the injection unit. The clamp is what actually holds the mold while the melted plastic is being injected, the mold is held under pressure while the injected plastic is cooling.
Next is the actual injection of the melted plastic. The plastic usually begins this process as pellets that are put into a large hopper. The pellets are then fed to a cylinder; here they are heated until they become molten plastic that is easily forced into the mold. The plastic stays in the mold, where it is being clamped under pressure until it cools.
The next couple of steps consist of the dwelling phase, which is basically making sure that all of the cavities of the mold are filled with the melted plastic. After the dwelling phase, the cooling process begins and continues until the plastic becomes solid inside the form. Finally, the mold is opened and the newly formed plastic part is ejected from its mold. The part is cleaned of any extra plastic from the mold.
As with any process, there are advantages and disadvantages associated with plastic injection molding. The advantages outweigh the disadvantages for most companies; they include being able to keep up high levels of production, being able to replicate a high tolerance level in the products being produced, and lower costs for labor as the bulk of the work is done by machine. Plastic injection molding also has the added benefit of lower scrap costs because the mold is so precisely made.
However, the disadvantages can be a deal breaker for smaller companies that would like to utilize plastic injection molding as a way to produce parts. These disadvantages are, that they equipment needed is expensive, therefore, increasing operating costs.
Thankfully, for these smaller companies, there are businesses that specialize in custom plastic injection molding. They will make a mock up mold to the exact specifications, run it through the complete process and present the completed piece along with an estimate to complete the job to the customer.
Linda Moore writes on a variety of subjects including home ownership, travel, personal enrichment, plastic injection molding and replacement auto glass
Find More Plastic Injection Articles
how do you take off the plastic piece on injection needles?
Question by DaniDisaster.: how do you take off the plastic piece on injection needles?
i’m piercing my monroe and to avoid possible scarring..
i was wondering if anyone knows how to take off the little plastic piece on injection needles.
(..ohh and i know i should probably get an actual piercing needle, but i don’t want to wait that long)
((and also if you have any objections.. I DON’T WANT TO HEAR THEM:))
Best answer:
Answer by ѕwεετ ηστнιηgѕ
Do the smart & responsible thing: go to a professional to get it done.
Injection needles aren’t meant for piercings.
Know better? Leave your own answer in the comments!
china plastic injection molding, injectin moulding
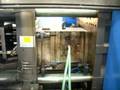
(webmaster@cnmoulding.com) high precision part with thread,because customer not allow the fix insert to let mould automatically working, so we have to design with manually. customer request is always what we should to do. we change follow customer change, visit www.cnmoulding.com for detail
Im not sure the exact day they installed these but during my visit on 7/18 I noted at least 8 of these machines around busch gardens. This video was taken just outside of jungala. The video doesnt capture the tiger well but it sure does show the machine is definately either a refurbished model or brand new. If indeed busch gardens is bringing this back than I wonder if they have similar plans for other parks. Either way this is definately a curiousity to bring back even as busch gardens looks about ready to be sold to someone else.
Video Rating: 3 / 5
The Processible Plastic for Mold Making
The Processible Plastic for Mold Making
1. Introduction
The processible plastic — Hongke material is a fundamental casting material with high density, high precision and high stability and is suitable for cutting in high speed. It is widely used abroad in aviation, navigation stage properties, and electrical appliance where high quality mold and module are required.
Concurrently, only few countries in the world are able to produce this kind of processible plastic. With the development of high technology, the demand for high quality mold with a complicated curve shape, and difficult technique in manufacturing is increasing, As a result of their own limitation, the traditional casting material such as plaster, paraffin and wood etc, can not realize CNC numerical control rnanufactuimg and satisfy the need for development. Therefore the processible plastic replaces the primeval mold making material. Particularly in the 90’s, with rhe spread of numerical control manufacturing technique, the phenomenon is even more outstanding. In early 80’s, similar materials has been invented for smiuktmg cutting arid mold making on numerical control machine, but in our country this kmd of material relied totally on import until 1997. This fully demonstrated the importance of this kind of material for our mold making industry. For example mold making,casting mould,plastic injection mold etc.According to statistics, till April 1998, we have already 400 set of numerical control center (5 axises, 5 axises) of our mold making industry. It showed product simulating cutting requiring processible plastic. The demand is evident. As specified in 95 national plan, the annul output after 2000 of automobile will reach 2 million 7 hundred. Some 175 to 440 kinds of basic body type of automobile will leave for renovation and reform. The cycle for automobile type renewal is 6-10 years in our country. In the foreseen years the processible plastics will be used more extensively in life. Therefore the processible plastics – Hongke plastics is produced to meet the demand, its performance index has already reached the international standard for likewise products.
2. Develop of the product
At the moment, only few countries are able to manufacture processible plastics worldwide. Before 97, china has spent over tens of millions US dollars on this material. To produce and nationalized the material and to cut the cost and replace the import products become urgency. It’s a common knowledge that mold-making industry is the mother of modern industry. It is a significant symbol of industry development of the country. One cannot separate the development of mold material when talking about mold making. In the recent years, our mold making industry is transiting into modem industry development, CAD/CAM technique, numerical control manufacturing are widely used, consequently the requirement for the mold material is higher. Once a technician of a famous mold workshop discuss with us about producing a kind of basic casting material for high speed cutting on the numerical control machine, which should not be transfigured by the process,
of which the amount of abrasion of the knife should be low, and doesn’t absorb moisture
and is antisepsis, with a sufficient degree of finish on the surface^ and be preservable over
long-term. The factory is allocated with CAD/CAM technique together with advanced
numerical control manufacturing center. But the so-called ” processible material” has been
relied on import, which is expensive to buy and gives a long cycle for supplying. Hence we
made a survey over the mold making industry, and the result verified that the material has
a potential huge market. At that time, no such material was available nationwide, it is totally
relied on import. Therefore Honke material co. Ltd. began to engage itself on the research
and development of the material, during the formulation of the prescription, through
selecting various chemical structure of macromolecule to adjust, modify, and add ancillary
preparations and filling, can prepare double component mash like material and panel
material of different high and low density and performance index. When basal material is in
the basic system of macromolecule, add different modification monomer material of all
conditions, such as elasticizer, activator, and filling etc can greatly improve the
technical performance of the processibel material. Below is a brief description at initial period of matching the material and reaction procedure.
Of which Rl – diphenol U- ammonia ester conjunction radical
R- radical or hydrogen – position of activity core
Hongke processible plastics has been identified as the provincial new product in 12, 1999, the serial number is Liao Jing ke jian zi No. 991072. The unified conclusion of Slie experts is Hongke processible plastic is the initiate of the country, which reaches the: International standard and can compete with the congener products abroad. Aftei Hcrgke processible material came into market, by 2-year trial making rind sdiing, it gained the praise of the industry and is able to replace the products of same category abroad. For example mold making,casting mould,plastic injection mold etc
3.pracal applicalions
As for automobile bumper, application of Hongke 970850 processible plastic, which has a unique rough integrated design, is the mold structure not available abroad, and it does not require bonding. From the product design we understand that mold material which have the following characteristics 1. Spare material 2. Save cost 3. Save the manufacturing time, are considered highly by the companies of the industry.
4.features and function
Hongke material is attaining credits from the industry for 3 great characteristics, which are
easy to manufacture, high stability and low cost. The of the material, accommodates
the need for the development of the industry, shorten the mold making period, lower the cost and raise the precision. Copy the mold with the original, the material selected for copying the mold doesn’t shrink, the stability of the dimension is sound, the adopted material has no ill effect on the original metal and non metal mold, easy for clean, has no limit on the dimension of the copied model, can adjust the time for mold making at will, Hong Ke Material guarantees the uniformed solidity of the copied mold, it is a beneficiary for the outside dimension of the whole mold, and raise greatly the quality of the mold product.
4.1 High precision, light weighted, applicable for all kinds mold design.
4.2 High precise processible plastics, easy to manufacture manually or by machine, high stability of the dimension.
4.3 Affirm CAD/CAM program, mold design, compound mold, and simulate structure mold.
4.4 Main mold fabricate, basal mold fabricate, copy mold, cast mold and clamp.
4.5 Use under the condition of rotate speed of 1 OOOrpm/min of the knife in milling
center, Hongke product is not disfigured or destroyed etc.
4.6 Appropriate rigidity, use 0.66mm milling cutting, with a depth of 10mm, chip removal is normal, long life of the knife.
4.7 After Hongke processible plastics is manufactured, the surface of the material has a high degree of finish, it is suitable for post orders techniques such as and spray painting.
4.8 The measurement of the reproduced mold has a high stability, the made clamp performance has already reached the performance index of like products abroad.
Hongke Material density 078g/ cm3
Qiba Material density 0.77g/cm3
Thermal expansion
Name Temperature Relative elongation indicator Average linear
expansion coefficient
°C X L0 ~ * X 10 ~ e/ °C
Qiba Material 20 0 0
Hongke Material 20 0 0
Qiba Material 50 1.643 41.1
Hongke Material 50 1. 682 51.1
Qiba Material 60 1.794 52.1
Hongke Material 60 2. 201 55. 9
Bend Resistant Strength obb (test condition span 30mr, indenter diameter 20mm)
Name Color of the Sample Sena resistant strength bbb(mpa) Sample
measurement # 25
Hongke Materia! white 32
Hong Kong Material red 26
Pressure Resistant Strength
Name Color of the sample y
Hongke Material white pressure resistant strength is 26 tbb -,
Hong Kong Material red when reach pressure resistant strength 25, Djrt?
bbb destabilized.
David ZHENG is the CEO of http://www.cikmold.com. An ISO 9001 certified enterprise speciality in casting mould,mold making,plastic injection mold etc.
i need information about thin sheet plastic injection molding?
Question by sarfraz m: i need information about thin sheet plastic injection molding?
Best answer:
Answer by Joe S S
Will vacuum forming do?
http://www.thermofab.com/vacuum_forming.html
Give your answer to this question below!
PLASTIC INJECTION
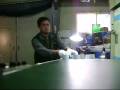
VIDEO OF EPS PINOY KOREA
www.jiyang.com.tw Tel: 886-4-26881297 Founded in 1986, Ji Yang is a professional plastic mold injection factory, specializing in manufacturing various kinds of buckles used by traveling suitcases, backpacks, and duffel bags, etc.; accessories for ready-made clothing and shoes, auto parts and medical equipments. Our products are produced at highest quality to meet every customer-demands. State-of-the-art technology and solid management accompanied with continuous innovation have earned high credibility and reliability for us. Our products also include buckle, cord lock, PVC protector, shoulder pad, side wheel, handle, eyelet, cart system as well as other plastic products. Advanced machining, R&D and emphasis on quality control ensure good quality for customer rights. Please visit our website for more details.
All You Need To Know About Plastic Moulding
All You Need To Know About Plastic Moulding
We cannot imagine a world without plastics. Plastics have found their importance in almost all application ranging from household items to complicated research equipments. Though there were controversies that the plastics pose a threat to the environment, the advancements in plastic manufacturing technologies have given birth to the eco-friendly plastics. Plastic manufacturers can now recycle and create new plastic products out of the used plastics. You will be well aware of the fact that injection moulding is widely used to manufacture the plastic products. Today’s plastic moulding is very much advanced and very different from what was originally invented. Just keep on reading the article to know all about the plastic moulding techniques.
A Little History
Plastic moulding is not a new concept developed in the 21st century. Moulding plastics into useful products exits since the origin of manmade plastic in the year 1851. The process of heating plastics and melting the molten material to obtain the shape of the mould is the basic concept behind plastic moulding. Though the concept of plastic moulding remains the same today, this technology has seen many advancements. Plastic moulding received huge importance during the period of Second World War due to the demand for the plastic medical equipments. Infact the plastic manufacturers where struggling to meet the demand for the plastic products during this period. This is period when the plastic moulding industry got a new shift towards development.
Current Plastic Moulding Techniques
Though the main concept of plastic moulding remains the same, the equipments used by the plastic manufacturers have changed a lot. With the integration of latest computer technologies the production rate of plastic moulding is greatly increased today. Unlike the olden days only when only fresh plastic materials were moulded to useful products, today with environmental awareness on the rise, plastic moulding concentrates on using recycled materials. Moreover, the advancements in plastic moulding technology has made it possible to manufacture products in any complicated shapes.
The Applications Of Modern Plastic Moulding
The applications of plastic injection moulding are virtually unlimited. Starting from simple plastic carry bags to complicated lifesaving devices – every plastic product manufactured today are through plastic injection moulding. Some of the common applications of plastic moulding are the manufacturing of products such as packaging bags, automobile parts, beverage cans and bottles, computer accessories etc.
The Future Of Plastic Moulding
You will be well aware of the fact that the use of plastics is banned in certain areas of all countries. People think that this may end the plastic manufacturing as environmental pollution is a major concern today. However, with the introduction of the recyclable plastics, the plastic industry has got a rebirth. Afterall, as already said, we cannot imagine a world without plastics.
R.E Davison is known in industy by two leading brands: RED Composites and Gloda Manufacturing and offer services in 2 major areas including plastic moulding. RED Composites for Thermoset plastic and plastic injection moulding for metal pressing and deep drawing for both the Australian and export market.
Related Plastic Injection Articles
Plastic Injection Molding Suggestions?
Question by Filosun: Plastic Injection Molding Suggestions?
I plan on making a large plastic tray, HDPE (overall 26″ x 20″ x .5″)
The main panel area will be a mesh design with trapezoid/diamond shaped holes. Each hole will have 4 sides 2″ each with angles 60°, 120°,60°, 120°.
The mesh will be 0.08″ thick and 0.7″ wide.
I figure such a flat item with large surface area and thin pathways will be difficult for plastic to flow through, and I dont’ want to heat it up too much because I’ve run into shrinkage problems before.
Right now I’m thinking 450 tons or 600 tons of force, not sure about how many injection points.
Does anybody have any suggestion for how much pressure I should apply and if I need multiple injection points?
Best answer:
Answer by miggitymaggz
A picture of your tray (or 3D image) would be beneficial here.
From justifying that you have thin pathways and complex shaped holes, multiple injection sites are a probably a good idea to avoid weld lines or cold fronts, flow lines, voids, etc.
Depending on the viscosity of your resin, heat, etc. will also determine # of injection sites. There are analysis tools for composite flow, which can predict where defects are most likely to occur.
What do you think? Answer below!
china mould, plastic injection moulding
www.cnmoulding.com ,who can give us some suggestion how to solve the problem for so big deformation when we use HDPE material, if use ABS,no anyproblem, four point hotter runner a lot of ribs at back side
Video Rating: 0 / 5
plastic bags manufacturing -LMT- Lashen Plast
Video Rating: 5 / 5