Posts Tagged ‘molds’
Making Castaldo Rubber Jewelry Mold Cutting Bracelet Molds
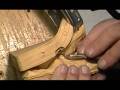
This is a demonstration on how to cut a castaldo rubber bracelet mold for the lost wax jewelry casting mass production process.
Video Rating: 4 / 5
Injection tooling, Injection mold, silicone rubber, rubber molds, mold maker,injection moulding.
Injection tooling – Customer design service. – Prototyping. – Mold making. – Manufacturing process control. – Mold flow analysis service available ! – Reverse engineering. – Customer molding & assembly. – Cold runner mold and hot runner mold (MoldMaster, Incoe, Masterflow, LKM,…
Video Rating: 0 / 5
Creating complex slide molds are simple with Solid Edge
Watch how easy it is to create a complex mold that requires a slide using Solid Edge Mold Tooling.
Video Rating: 3 / 5
RGE China – Automatic Loading of Washers in Armrest Plastic Injection Moulding
Video Rating: 0 / 5
Injection Molds and Rotational Molds – Manufacturing For a Demanding Marketplace
Injection Molds and Rotational Molds – Manufacturing For a Demanding Marketplace
The world has become very dependent upon plastic products. From household items to industry and aerospace, plastic in its many formulations has transformed modern manufacturing and created conveniences and economies unimagined in the early decades of the 20th century.
Injection Molds
The injection molding industry took hold in 1946 when James Hendry built a screw injection molding machine. But, his technology was based on an earlier invention by John Wesley Hyatt who, in 1868 injected hot celluloid into a mold to make billiard balls. Hyatt’s method used a plunger to force the material inside a mold. Hendry’s improvement was revolutionary because it eliminated the plunger and replaced it with an auger-type action that better distributed material and facilitated the use of plastic inside molds.
Today’s injection molds use much the same process and produce a wide variety of products from car panels to outdoor furniture, small toys and tools. Injection molding is ubiquitous in manufacturing and uses many different materials from polymer plastics to aluminum, copper and other metals. The plastic bottles and kitchen implements people use in everyday life are products of the injection process.
Because the metal molds are generally expensive to produce, injection molding is most economically used when thousands of pieces are being manufactured. Molds are made of hardened steel or, more recently, aluminum which is less expensive.
The Injection Process
Described very simply, molten plastic is injected into the mold under high heat and pressure. The goal is to have the molten plastic material evenly flow to all parts of the mold, creating an exact, consistent, solid plastic replica of the mold cavity. After a brief cooling cycle, the mold or tooling mechanically ejects the plastic part which then moves on through the manufacturing process. In the injection molding industry, this is a completely automated process that’s very fast and extremely efficient.
Rotational Molding
Rotational molding is yet another method of producing multiple products, most often made with a variety of plastic powders. This process is usually used in making hollow products such as traffic cones, canoes, kayaks, bicycle helmets and giant tanks used for water or chemical storage.
Like Injection molding, rotational molding had its roots in the 1940s. But it was not until the technology was more sophisticated and new polymer and plastic formulations became available that the rotational process became a mainstream manufacturing method.
Rotational Process
The two processes are quite different. Let’s consider, for example, a 300 gallon water storage tank made of polyethylene. Picture a master mold made of aluminum or steel. The plastics manufacturer pours poly resin powder into the mold that is fitted inside an oven. Once sealed, the mold is mechanically turned on at least three axes, moving much like a gyroscope. At the same time, the oven is raised to an appropriate temperature and the polymer – or other material – tumbles inside and slowly coats the inner walls of the mold, melting as it rotates.
Once the optimal temperature is reached, the mold is cooled. As the temperature of the mold itself falls, the product on the inside shrinks away from the inner walls and is easily removed. This is not always the case with injection molds that are often more difficult to successfully remove. The shrinking action of rotational molding is particularly desirable when the product is very large and awkward to handle.
Rotational molding is also more economical for some products because less material is used. In addition, the polymer that is left over from one mold can be used in another. The method itself is more streamlined than injection molding, which requires more interlocking parts.
Materials Improve and Expand
Most products made with the rotational molding method are from the polyethylene family. Other materials include nylons, polypropylene and PVC plastics. Some manufacturers have developed formulas that integrate the use of natural materials such as sand and chips of stone to make products.
Plastic and resin products are now an integral part of everyday life and supply us with items as tiny as paper clips and as big as storage tanks. As the industry developed, so too has environmental awareness about the safety and use of these petrochemical-based products. Today, materials can meet the specifications of FDA requirements, and other health and safety related regulations. Producers are also cooperating to create products that can be recycled.
Visit us for additional information on rotational molding and rotomolding equipment.
Prototype Injection Molding, Thermoplastic Injection Molding, Injection Molds
Prototype Injection Molding, Thermoplastic Injection Molding, Injection Molds
Hobart, Washington USA (Articles Base) July 15, 2008
The Prototype Injection Molding and Injection Molds Services is a new webpage that was just added to the new Rapid Prototyping Information Website that has just been released. This new Prototype Injection Molding Process webpage has all of the information you need to know on Injection Prototyping and Thermoplastic Injection Molding and the main information you need to know on Prototype Injection Molding. You can visit this Thermoplastic Injection Molding Services webpage at: http://www.prototypezone.com/plastic-injection-molding/
Here is an excerpt from the new Thermoplastic Injection Molding and Molds webpage:
“Rapid Prototyping is the process of automated manufacturing of physical components using solid freeform fabrication. They are used in a wide range of applications, everything from medical to fine art. Rapid Prototyping machine works by taking virtual models from software and then converting it into extremely thin, horizontal cross-sections and then goes onto create each of the cross-section in physical space in a cyclic manner until the model is completed. Rapid Prototyping is a WYSIWYG process in which the virtual model bears identical resemblance to the finished physical model. Additional fabrications allows the machine to lay down layers of sheet, liquid or powder material and build up a series of cross-sections These layers are finally automatically fused together to render the final product.
The main advantage of rapid prototyping is the ability to create any shape no matter how complex the geometry is. The commonly used data interface between the machine and the software is the STL format. It works by approximating the geometry of a part using triangular facets, smaller the facets higher will be the surface quality. The word “rapid” is used relative top conventional methods which take days to construct a model depending upon its complexity. Rapid prototyping can create the model within a few hours, though it is highly dependent of the type of machines and the size of the model. There have been several new technologies available for rapid prototyping including Fused Deposition Modeling, Selective laser sintering, 3D printing, and Electron Beam Melting.”
The new Thermoplastic Injection Molding page is free information to members and non-members and can be found at: http://www.prototypezone.com/injection-molding/. However, users of Prototype Zone who decide to be members can join for free and receive two free E-Books on Rapid Prototyping for a limited time offer. Prototype Zone will be adding new information all the time on Rapid Prototyping so check back often in the forum and blog for the latest information at: http://www.prototypezone.com/plastic-molds/
About Prototype Zone: Prototype Zone is the leading information source and community website for all things about Prototyping and Rapid Prototyping. Visit the website to join for free and receive two free ebooks on Rapid Prototyping for a limited time offer.
Author: Ryan Rounder, Director of PR
Email: Pressreleases@prototypezone.com
Website URL: http://www.prototypezone.com
Phone: 425-503-8401
City/State: Seattle, Washington
How does soft plastic injection molds work?
Question by trout_tapout: How does soft plastic injection molds work?
Best answer:
Answer by MJ23_4life
I hope this helps:
http://pslc.ws/macrog/kidsmac/molding.htm
Know better? Leave your own answer in the comments!
Plastic Injection Molds
Watch more @ www.sme.org
Video Rating: 4 / 5
www.controlplastics.com – In this video you are seeing a robot remove the part from the machine and place it on a conveyor belt where it will take it to a machine operator who will inspect the part and then place it into a box. The part being made in this video is a baby bottle, on another machine, a cap and cover are being made that will make the bottle complete. Visit our website for more info on all our capabilities, and contact us for your next plastic or metal injection molding project.
Making Mold manufacturer,plastic injection molds,Mold making,liquid silicone rubber molds
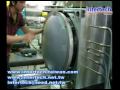
www.taiwanmoldmaker.com We make plastic injection molds, die-casting molds, silicone rubber molds, liquid silicone rubber molds, LSR molds, rubber molds, press molds and hot runner molds (MoldMaster, MasterFlow, LKM, Incoe systems…etc). We are especially good in dealing the undercut molds,…