Posts Tagged ‘making’
Plastics Directory: a Source for Captivating Products, or Technology for Making Such Products
Plastics Directory: a Source for Captivating Products, or Technology for Making Such Products
With its malleability (plasticity) and ability to accept different colors, plastic is a material that can convert even day-to-day utility articles into decor items. And a plastics directory is your one-stop resource for all kinds of highly saleable products (or the technology and equipment needed to make them).
A quick look at some typical plastic products reveals the huge variety possible.
The Compact Disc (CD) in your computer or video player
The jerry can you use to store different kinds of liquids
The kitchen balance you use to measure out cooking ingredients
The plastic film that shows off your products as they are
The intriguing and fascinating range of toys that your children, or you, play with
The sturdy components made with engineering plastic
Replicas that can reproduce an uncanny look of the originals, such as ivory carvings and silk clothing (rayon)
A good plastics directory is your source for products to sell (or use). Or if you prefer to produce the products, the plastics directory’s sections on plastic machineries, equipment and materials could help you locate several suppliers of these, and get competitive bids.
Plastics Directory – A Niche Directory
The discussion in the previous section illustrates how niche directories are particularly valuable for a niche audience. Persons interested in plastics products would find a plastics directory the ideal resource to locate products, equipment and ever services (like consultancy services) they are looking for.
Very often, the directories accommodate only businesses located in specific countries. For example, a UK Plastics Directory might only list suppliers in the UK. This is a way to promote the businesses in one’s own country. In fact, such niche directories are sometimes produced by regional development agencies seeking to promote the development of specific industries in their regions.
Another way such niche directories provide value to their users is through specialized categories. Whereas a general business directory might have a single category like plastics, or a few categories like plastic machinery, plastic products and plastic materials, a niche directory could have more elaborate categorization.
For example, here is one classification system adopted by a plastics directory:
Plastic Films
Plastic Flow Control Equipment
Plastic Hardware
Plastic Injections Molding Tooling & Services
Plastic Materials
Plastic Packaging Machines, Equipment & Supplies
Plastic Products
Plastic Raw Materials & Supplies
Plastic Safety Equipment
Plastic Sheeting
Resins
(Source: http://www.plastics-malaysian.com/ )
It would be evident that with the above kind of categorization, specific users could organize their searching much more purposefully.
One way for the niche directories to add even more value is through how-to articles, market news and other resources of business interest. Such a plastics directory could be a complete resource for those interested in plastics.
Conclusion
A plastics directory is a good example of a niche directory. Such niche directories could provide much greater value to a niche audience than a general business directory. For example, more specialized and elaborate classification, tailored to the particular industry, would help readers to quickly locate the precise products or services they want. Supplemented with how-to articles, market development news, and such resources, these niche directories could add even more value.
Daniel Frenchy is with businessmagnet, an award winning business plastics directory listing over 70,000 businesses offering over 20,000 products and services. The directory indexes listings by company, town, postcode and product, making it very user-friendly.
Related Plastic Injection Articles
Making Plastic – Plastic Moulding
Making Plastic – Plastic Moulding
Ever wondered how plastic is moulded into the exceptionally useful things that we employ in our daily life? Is it as simple as melting plastic and lathering the sides of a mould with it and cooling it, much like chocolate? The answer, actually, is no. Moulding plastic is a little more complex than that. Plastic is made using a process often called plastic injection moulding.
What is this type of moulding
Plastic injection moulding is the method of manufacturing parts made of thermoplastic and thermosetting plastic by melting and forcing into moulds where they cool to form the desired object.
How does plastic injection moulding work?
The process of plastic injection moulding usually begins with an industrial designer or engineer who designs a product. This is followed up by the work of a toolmaker or mould maker who makes the mould to fit the design created. These moulds are metallic and usually made using either steel or aluminum.
Using machines, they are made to acquire the exact shape desired by the design. Once this is done, the process of actually making the plastic follows. This involves thermoplastic and thermosetting plastic being fed into a heated barrel and mixed. This melted material is then forced into the cavity of a mould and there it cools and hardens to form the desired part.
Some characteristics of the process:
1. I uses melted and mixed thermoplastic or thermoset plastic as the base
2. It uses a plunger which acts like a screw or a ram to force the melted material in the mould
3. It makes a shape that is open-ended and has taken the shape of the cavity of the mould
4. It shows a parting line and gate marks on the finished products and the ejector pin marks can also usually be made out
Some history
Alexander Parkes invented plastic in 1851 in Britain. This was worked on and bettered by John Hyatt, an American inventor in 1868. He also patented, in 1872, the first injection moulding machine. In the 1940s, the need for mass production of plastic products increased and saw the invention of the first screw injection machine by inventor James Hendry of America. This increased not only the speed of production but also the amount of precise control that could be exercised on the finish of the product.
Since then, this type of moulding has been used widely in the production of everything right from milk cartons to entire car panels and automotive parts. Since it is not a very costly material, it is best suited for mass produced goods.
Advantages of this type of moulding:
1. The rate of production are very high and therefore mass production is much benefitted
2. Since tolerance levels are high, they can be repeated
3. The labour cost is very low
4. The losses in scrap are very minimal
5. The products require very minimal finishing
6. A wide range of materials can be used
Disadvantages using this type of moulding:
1. Although labor expense and scrap loses are minimal, the cost of equipment and therefore investment is high
2. The running costs have the potential to be high
3. There is also need to design the correct parts
longxiang-ltd.com is The TOP 1 Plastic mould store,we sell rapid prototypes,you can buy Safe Plastic mold and Rapid prototype from us.
The Processible Plastic for Mold Making
The Processible Plastic for Mold Making
1. Introduction
The processible plastic — Hongke material is a fundamental casting material with high density, high precision and high stability and is suitable for cutting in high speed. It is widely used abroad in aviation, navigation stage properties, and electrical appliance where high quality mold and module are required.
Concurrently, only few countries in the world are able to produce this kind of processible plastic. With the development of high technology, the demand for high quality mold with a complicated curve shape, and difficult technique in manufacturing is increasing, As a result of their own limitation, the traditional casting material such as plaster, paraffin and wood etc, can not realize CNC numerical control rnanufactuimg and satisfy the need for development. Therefore the processible plastic replaces the primeval mold making material. Particularly in the 90’s, with rhe spread of numerical control manufacturing technique, the phenomenon is even more outstanding. In early 80’s, similar materials has been invented for smiuktmg cutting arid mold making on numerical control machine, but in our country this kmd of material relied totally on import until 1997. This fully demonstrated the importance of this kind of material for our mold making industry. For example mold making,casting mould,plastic injection mold etc.According to statistics, till April 1998, we have already 400 set of numerical control center (5 axises, 5 axises) of our mold making industry. It showed product simulating cutting requiring processible plastic. The demand is evident. As specified in 95 national plan, the annul output after 2000 of automobile will reach 2 million 7 hundred. Some 175 to 440 kinds of basic body type of automobile will leave for renovation and reform. The cycle for automobile type renewal is 6-10 years in our country. In the foreseen years the processible plastics will be used more extensively in life. Therefore the processible plastics – Hongke plastics is produced to meet the demand, its performance index has already reached the international standard for likewise products.
2. Develop of the product
At the moment, only few countries are able to manufacture processible plastics worldwide. Before 97, china has spent over tens of millions US dollars on this material. To produce and nationalized the material and to cut the cost and replace the import products become urgency. It’s a common knowledge that mold-making industry is the mother of modern industry. It is a significant symbol of industry development of the country. One cannot separate the development of mold material when talking about mold making. In the recent years, our mold making industry is transiting into modem industry development, CAD/CAM technique, numerical control manufacturing are widely used, consequently the requirement for the mold material is higher. Once a technician of a famous mold workshop discuss with us about producing a kind of basic casting material for high speed cutting on the numerical control machine, which should not be transfigured by the process,
of which the amount of abrasion of the knife should be low, and doesn’t absorb moisture
and is antisepsis, with a sufficient degree of finish on the surface^ and be preservable over
long-term. The factory is allocated with CAD/CAM technique together with advanced
numerical control manufacturing center. But the so-called ” processible material” has been
relied on import, which is expensive to buy and gives a long cycle for supplying. Hence we
made a survey over the mold making industry, and the result verified that the material has
a potential huge market. At that time, no such material was available nationwide, it is totally
relied on import. Therefore Honke material co. Ltd. began to engage itself on the research
and development of the material, during the formulation of the prescription, through
selecting various chemical structure of macromolecule to adjust, modify, and add ancillary
preparations and filling, can prepare double component mash like material and panel
material of different high and low density and performance index. When basal material is in
the basic system of macromolecule, add different modification monomer material of all
conditions, such as elasticizer, activator, and filling etc can greatly improve the
technical performance of the processibel material. Below is a brief description at initial period of matching the material and reaction procedure.
Of which Rl – diphenol U- ammonia ester conjunction radical
R- radical or hydrogen – position of activity core
Hongke processible plastics has been identified as the provincial new product in 12, 1999, the serial number is Liao Jing ke jian zi No. 991072. The unified conclusion of Slie experts is Hongke processible plastic is the initiate of the country, which reaches the: International standard and can compete with the congener products abroad. Aftei Hcrgke processible material came into market, by 2-year trial making rind sdiing, it gained the praise of the industry and is able to replace the products of same category abroad. For example mold making,casting mould,plastic injection mold etc
3.pracal applicalions
As for automobile bumper, application of Hongke 970850 processible plastic, which has a unique rough integrated design, is the mold structure not available abroad, and it does not require bonding. From the product design we understand that mold material which have the following characteristics 1. Spare material 2. Save cost 3. Save the manufacturing time, are considered highly by the companies of the industry.
4.features and function
Hongke material is attaining credits from the industry for 3 great characteristics, which are
easy to manufacture, high stability and low cost. The of the material, accommodates
the need for the development of the industry, shorten the mold making period, lower the cost and raise the precision. Copy the mold with the original, the material selected for copying the mold doesn’t shrink, the stability of the dimension is sound, the adopted material has no ill effect on the original metal and non metal mold, easy for clean, has no limit on the dimension of the copied model, can adjust the time for mold making at will, Hong Ke Material guarantees the uniformed solidity of the copied mold, it is a beneficiary for the outside dimension of the whole mold, and raise greatly the quality of the mold product.
4.1 High precision, light weighted, applicable for all kinds mold design.
4.2 High precise processible plastics, easy to manufacture manually or by machine, high stability of the dimension.
4.3 Affirm CAD/CAM program, mold design, compound mold, and simulate structure mold.
4.4 Main mold fabricate, basal mold fabricate, copy mold, cast mold and clamp.
4.5 Use under the condition of rotate speed of 1 OOOrpm/min of the knife in milling
center, Hongke product is not disfigured or destroyed etc.
4.6 Appropriate rigidity, use 0.66mm milling cutting, with a depth of 10mm, chip removal is normal, long life of the knife.
4.7 After Hongke processible plastics is manufactured, the surface of the material has a high degree of finish, it is suitable for post orders techniques such as and spray painting.
4.8 The measurement of the reproduced mold has a high stability, the made clamp performance has already reached the performance index of like products abroad.
Hongke Material density 078g/ cm3
Qiba Material density 0.77g/cm3
Thermal expansion
Name Temperature Relative elongation indicator Average linear
expansion coefficient
°C X L0 ~ * X 10 ~ e/ °C
Qiba Material 20 0 0
Hongke Material 20 0 0
Qiba Material 50 1.643 41.1
Hongke Material 50 1. 682 51.1
Qiba Material 60 1.794 52.1
Hongke Material 60 2. 201 55. 9
Bend Resistant Strength obb (test condition span 30mr, indenter diameter 20mm)
Name Color of the Sample Sena resistant strength bbb(mpa) Sample
measurement # 25
Hongke Materia! white 32
Hong Kong Material red 26
Pressure Resistant Strength
Name Color of the sample y
Hongke Material white pressure resistant strength is 26 tbb -,
Hong Kong Material red when reach pressure resistant strength 25, Djrt?
bbb destabilized.
David ZHENG is the CEO of http://www.cikmold.com. An ISO 9001 certified enterprise speciality in casting mould,mold making,plastic injection mold etc.
Making Plastic Mold-Plastic Injection Moulding
Making Plastic Mold-Plastic Injection Moulding
Ever wondered how plastic is moulded into the exceptionally useful things that we employ in our daily life? Is it as simple as melting plastic and lathering the sides of a mould with it and cooling it, much like chocolate? The answer, actually, is no. Moulding plastic is a little more complex than that. Plastic is made using a process often called plastic injection moulding.
What is this type of moulding
Plastic injection moulding is the method of manufacturing parts made of thermoplastic and thermosetting plastic by melting and forcing into moulds where they cool to form the desired object.
How does plastic injection moulding work?
The process of plastic injection moulding usually begins with an industrial designer or engineer who designs a product. This is followed up by the work of a toolmaker or mould maker who makes the mould to fit the design created. These moulds are metallic and usually made using either steel or aluminum. Using machines, they are made to acquire the exact shape desired by the design. Once this is done, the process of actually making the plastic follows. This involves thermoplastic and thermosetting plastic being fed into a heated barrel and mixed. This melted material is then forced into the cavity of a mould and there it cools and hardens to form the desired part.
Some characteristics of the process:
1. I uses melted and mixed thermoplastic or thermoset plastic as the base
2. It uses a plunger which acts like a screw or a ram to force the melted material in the mould
3. It makes a shape that is open-ended and has taken the shape of the cavity of the mould
4. It shows a parting line and gate marks on the finished products and the ejector pin marks can also usually be made out
Some history
Alexander Parkes invented plastic in 1851 in Britain. This was worked on and bettered by John Hyatt, an American inventor in 1868. He also patented, in 1872, the first injection moulding machine. In the 1940s, the need for mass production of plastic products increased and saw the invention of the first screw injection machine by inventor James Hendry of America. This increased not only the speed of production but also the amount of precise control that could be exercised on the finish of the product.
Since then, this type of moulding has been used widely in the production of everything right from milk cartons to entire car panels and automotive parts. Since it is not a very costly material, it is best suited for mass produced goods.
Advantages of this type of moulding:
1. The rate of production are very high and therefore mass production is much benefitted
2. Since tolerance levels are high, they can be repeated
3. The labour cost is very low
4. The losses in scrap are very minimal
5. The products require very minimal finishing
6. A wide range of materials can be used
Disadvantages using this type of moulding:
1. Although labor expense and scrap loses are minimal, the cost of equipment and therefore investment is high
2. The running costs have the potential to be high
3. There is also need to design the correct parts
With the development of the market, the diversification of molding methods and new plastic materials would be developed in the future. In order to meet the needs of the market, whether plastic mold species, structure, performance or processing are bound to faster development. What’s more such a development must keep pace with the times.
longxiang-ltd.com is The TOP 1 Plastic mould store,we sell rapid prototypes,you can buy Safe Plastic mold and Rapid prototype from us.
Making Mold manufacturer,plastic injection molds,Mold making,liquid silicone rubber molds
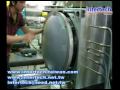
www.taiwanmoldmaker.com We make plastic injection molds, die-casting molds, silicone rubber molds, liquid silicone rubber molds, LSR molds, rubber molds, press molds and hot runner molds (MoldMaster, MasterFlow, LKM, Incoe systems…etc). We are especially good in dealing the undercut molds,…
What kind of pipe is used in making plastic injection moulding machine?
Question by momin_moin2006: What kind of pipe is used in making plastic injection moulding machine?
I want to know whether seamless pipes are used in making plastic injection moulding machine
Best answer:
Answer by Bert K
Yes, seamless pipes are used.
http://www.google.com/search?hl=en&client=firefox&hs=JyI&rls=com.yahoo%3Aen-US%3Aofficial&q=are+seamless+pipes+used+in+making+plastic+injection+moulding+machine&btnG=Search&aq=f&aqi=&aql=&oq=&gs_rfai=
.
Know better? Leave your own answer in the comments!