Posts Tagged ‘Made’
RJ BILLET ALUMINUM Powder Coated CLOCK CNC Milled WITH YOUR NAME CUSTOM MADE USA 1
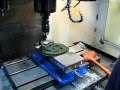
Do you needUSA extreme machining cnc machine work or USA aluminum zinc brass Molding or USA Plastic injection molding or USA water jetting done on a project? We have simplified this process so anyone can get it done. Please visit our web site for more information & products. www.vendio.com To receive a 5% discount please tell them the Shark sent you. In addition, tell them were you saw the add at. Like YOUTUBE. Come down & visit us at H&S Machine 3403 South 1400 West Suite B West Valley City, Utah, 84119-4050 Phone Gregg 801-755-7627 machine shop foreman PLEASE LEAVE A NAME & # WE DO NOT ALWAYS GET TO THE PHONE IN TIME. We are open MS 9 am to 7 pm mountain time. Send all questions & prints to hsmachinegregg@gmail.com If you need parts made in the USA by real professionals PLEASE INCLUDE YOUR 411 info… NAME & YOUR PHONE # IN ALL CORRESPONDENCE. WE CANNOT CONDUCT BUSINESS WITH YOU WITH OUT IT! MENTION WHERE YOU SAW THIS ADD & RECEIVE A 5% DISCOUNT WHEN YOU STOP BY OUR PLACE OF BUSINESS.
Video Rating: 0 / 5
Do you needUSA extreme machining cnc machine work or USA aluminum zinc brass Molding or USA Plastic injection molding or USA water jetting done on a project? We have simplified this process so anyone can get it done. Please visit our web site for more information & products. www.vendio.com To receive a 5% discount please tell them the Shark sent you. In addition, tell them were you saw the add at. Like YOUTUBE. Come down & visit us at H&S Machine 3403 South 1400 West Suite B West Valley City, Utah, 84119-4050 Phone Gregg 801-755-7627 machine shop foreman PLEASE LEAVE A NAME & # WE DO NOT ALWAYS GET TO THE PHONE IN TIME. We are open MS 9 am to 7 pm mountain time. Send all questions & prints to hsmachinegregg@gmail.com If you need parts made in the USA by real professionals PLEASE INCLUDE YOUR 411 info… NAME & YOUR PHONE # IN ALL CORRESPONDENCE. WE CANNOT CONDUCT BUSINESS WITH YOU WITH OUT IT! MENTION WHERE YOU SAW THIS ADD & RECEIVE A 5% DISCOUNT WHEN YOU STOP BY OUR PLACE OF BUSINESS.
Video Rating: 1 / 5
RJ BILLET ALUMINUM Powder Coated CLOCK CNC Milled WITH YOUR NAME CUSTOM MADE USA 8
Do you needUSA extreme machining cnc machine work or USA aluminum zinc brass Molding or USA Plastic injection molding or USA water jetting done on a project? We have simplified this process so anyone can get it done. Please visit our web site for more information & products. www.vendio.com To receive a 5% discount please tell them the Shark sent you. In addition, tell them were you saw the add at. Like YOUTUBE. Come down & visit us at H&S Machine 3403 South 1400 West Suite B West Valley City, Utah, 84119-4050 Phone Gregg 801-755-7627 machine shop foreman PLEASE LEAVE A NAME & # WE DO NOT ALWAYS GET TO THE PHONE IN TIME. We are open MS 9 am to 7 pm mountain time. Send all questions & prints to hsmachinegregg@gmail.com If you need parts made in the USA by real professionals PLEASE INCLUDE YOUR 411 info… NAME & YOUR PHONE # IN ALL CORRESPONDENCE. WE CANNOT CONDUCT BUSINESS WITH YOU WITH OUT IT! MENTION WHERE YOU SAW THIS ADD & RECEIVE A 5% DISCOUNT WHEN YOU STOP BY OUR PLACE OF BUSINESS.
Video Rating: 3 / 5
Video Rating: 5 / 5
CUSTOM CNC MADE COMPUTER CASE MOD 4
Do you need USA extreme machining cnc machine work or USA aluminum zinc brass Molding or USA Plastic injection molding or USA water jetting done on a project? We have simplified this process so anyone can get it done. Please visit our web site for more information & products. www.vendio.com To receive a 5% discount please tell them the Shark sent you. In addition, tell them were you saw the add at. Like YOUTUBE. Come down & visit us at H&S Machine 3403 South 1400 West Suite B West Valley City, Utah, 84119-4050 Phone Gregg 801-755-7627 machine shop foreman PLEASE LEAVE A NAME & # WE DO NOT ALWAYS GET TO THE PHONE IN TIME. We are open MS 9 am to 7 pm mountain time. Send all questions & prints to hsmachinegregg@gmail.com If you need parts made in the USA by real professionals PLEASE INCLUDE YOUR 411 info… NAME & YOUR PHONE # IN ALL CORRESPONDENCE. WE CANNOT CONDUCT BUSINESS WITH YOU WITH OUT IT! MENTION WHERE YOU SAW THIS ADD & RECEIVE A 5% DISCOUNT WHEN YOU STOP BY OUR PLACE OF BUSINESS.
Tabajando duro
Video Rating: 5 / 5
CUSTOM CNC MADE COMPUTER CASE MOD 8
Do you need a custom computer case? We have simplified this process so anyone can do it at home. Visit 1wonderfuldeals.com or email us at 1wonderfuldeals@gmail.com FOR SALE ON 1wonderfuldeals.com To buy it now. Do you need a USA custom computer case or USA extreme machining cnc machine work or USA aluminum zinc brass Molding or USA Plastic injection molding or USA water jetting done on a project? We have simplified this process so anyone can get it done. Visit 1wonderfuldeals.com or email us at 1wonderfuldeals@gmail.com Come down & visit us at Email us directly at hsmachinetom@gmail.com H&S Machine 3403 South 1400 West Suite B West Valley City, Utah, 84119-4050 Phone Tom (801) 686-8799 same # for 20+ years or Phone Gregg 801-755-7627 machine shop foreman PLEASE LEAVE A NAME & # WE DON’T ALWAYS GET TO THE PHONE IN TIME. We are open MS 9 am to 7 pm mountain time. Send all questions & prints to hsmachinetom@gmail.com if you need parts made in the USA by real professionals
Video Rating: 4 / 5
Multi-cavity Heated Platen hydraulic press from Beckwood Hydraulic Press Company used for flat sheet compression molding in a heat treating process for a major cleaning products manufacturer
Video Rating: 5 / 5
Plastic Injection Molding Made Easy- Downloadable!!
www.Universitypublishinghouse.net 90 large page book describes the process of molds, mold making, plastics, properties, sprues, runners, gates, plastic injection machines, more.
Video Rating: 1 / 5
How are car fenders made?
Question by Adam Cordell: How are car fenders made?
I’m wondering what the process is for mass producing car fenders (metal). I assume the plastic fenders are made from injection molding but the metal fenders are what fascinate me. Also does anyone know of a cheap method for reverse engineering a fender other then 3d scanning?
Best answer:
Answer by Kenny
With a million dollar stamping machine.
Add your own answer in the comments!
what is mouse made of ….the exact name of the material??
Question by boen h: what is mouse made of ….the exact name of the material??
i need to know what is the material of making a mouse and what process does it need ….injection molding or what ..
tell me asap
Best answer:
Answer by Ms. §exy
Mouse Anatomy
Body
The mouse’s “skin” is the outer, hard plastic body that the user guides across a flat surface. It’s “tail” is the electrical cable leading out of one end of the mouse and finishing at the connection with the Central Processing Unit (CPU). At the tail end, one to three buttons are the external contacts to small electrical switches. The press of a button closes the switch with a click; electrically, the circuit is closed, and the computer has received a command.
On the underside of the mouse, a plastic hatch fits over a rubberized ball, exposing part of the ball. Inside, the ball is held in place by a support wheel and two shafts. As the ball rolls on a surface, one shaft turns with horizontal motion and the second responds to vertical motion. At one end of each of the two shafts, a spoked wheel also turns. As these spokes rotate, infrared light signals from a light-emitting diode (LED) flicker through the spokes and are intercepted by a light detector. The dark and light are translated by phototransistors into electrical pulses that go to the interface integrated circuit (IC) in the mouse. The pulses tell the IC that the ball has tracked left-right and up-down, and the IC instructs the cursor to move accordingly on the screen.
The interface integrated circuit is mounted on the printed circuit board (PCB) that is the skeleton to which all the internal workings of the mouse are attached. The integrated circuit, or computer chip, collects the information from the switches and the signals from the phototransistors and sends a data stream to the computer.
Brain
Each mouse design also has its own software called a driver. The driver is an external brain that enables the computer to understand the mouse’s signals. The driver tells the computer how to interpret the mouse’s IC data stream including speed, direction, and clicked commands. Some mouse drivers allow the user to assign specific actions to the buttons and to adjust the mouse’s resolution (the relative distances the mouse and the cursor travel). Mice that are purchased as part of computer packages have the drivers built in or preprogrammed in the computers.
Raw Materials
The mouse’s outer shell and most of its internal mechanical parts, including the shafts and spoked wheels, are made of acrylonitrile butadiene styrene (ABS) plastic that is injection-molded. The ball is metal that is coated in rubber; it is made by a specialty supplier. The electrical micro-switches (made of plastic and metal) are also off-the-shelf items supplied by subcontractors although mouse designers can specify force requirements for the switches to make them easier or firmer to click. Integrated circuits or chips can be standard items, although each manufacturer may have proprietary chips made for use in its complete line of products. Electrical cables and overmolds (end connectors) are also supplied by outside sources.
The printed circuit board (PCB) on which the electrical and mechanical components are mounted is custom-made to suit the mouse design. It is a flat, resin-coated sheet. Electrical resistors, capacitors, oscillators, integrated circuits (ICs), and other components are made of various types of metal, plastic, and silicon.
Design
Design of a new mouse begins with meetings among a product development manager, designer, marketing representative, and consulting ergonomist (a specialist in human motion and the effects various movements have on body parts). A list of human factors guidelines is developed specifying size range of hands, touch sensitivity, amount of work, support of the hand in a neutral position, the user’s posture while operating the mouse, finger extension required to reach the buttons, use by both left- and right-handed individuals, no prolonged static electricity, and other comfort and safety requirements; these can differ widely, depending on whether the mouse is to be used in offices or with home computers, for example. A design brief for the proposed mouse is written to describe the purpose of the product and what it achieves; a look is also proposed in keeping with the anticipated market.
The design team returns to the table with foam models; scores of different shapes may be made for a single mouse design. User testing is done on these models; the engineers may do this preliminary testing themselves, or they may employ focus groups as typical users or observe one-on-one testing with sample users. When the selection of models is narrowed down, wooden models that are more refined and are painted are made of the winning designs. Input is gathered again on the feel, shape, and look of the models; the ergonomist also reviews the likely designs and confirms that the human factors guidelines have been achieved.
When the optimal model is chosen, the engineering team begins to design the internal components. A three-dimensional rendering is computer-generated, and the same data are used to machine-cut the shapes of the exterior shell with all its details. The mechanical and electronics engineers fit the printed circuit board (and its electronics) and the encoder mechanism (the ball, shafts, wheels and LED source and detector) inside the structure. The process of fitting the workings to the shell is iterative; changes are made, and the design-and-fit process is repeated until the mouse meets its design objectives and the design team is pleased with the results. Custom chips are designed, produced on a trial basis, and tested; custom electronics will help the design meet performance objectives and give it unique, competitive, and marketable characteristics.
The completed design diagrams are turned over to the project tooler who begins the process of modifying machines to produce the mouse. Tooling diagrams are generated for injection-molding the shell, for example. The size, shape, volume of the cavity, the number of gates through which the plastic will be injected into the mold, and the flow of the plastic through the mold are all diagramed and studied. After the final tooling plan is reviewed, tools are cut using the computer-generated data. Sample plastic shells are made as “try shots” to examine actual flow lines and confirm that voids aren’t induced. Changes are made until the process is perfect. Texture is added to the external appearance of the shell by acid etching or by sand blasting.
In the meantime, the engineering team has set up the assembly line for the new mouse design and conducted trial assemblies. When the design details are finalized, tools have been produced, and test results have met the design team’s objectives and standards, the mouse is ready for mass production.
The Manufacturing
Process
To make the computer mouse, several manufacturing processes are performed simultaneously to make different pieces of the unit. These processes are described in the first three steps below. The pieces are then brought together for final assembly, as described in steps 4 through 7.
In one of the sets of manufacturing and assembling steps, the printed circuit board (PCB) is cut and prepared. It is a flat, resin-coated sheet that can be of surface-mount design or through-hole design. The surface-mount version is assembled almost entirely by machine. A computer-controlled automatic sequencer places the electrical components in the proper order onto the board in a prescribed pattern.
For through-hole PCB assembly, attachment wires of the electronic components are inserted in holes in the PCB. Each assembly line worker has a drawing for part of the board and specific units to add. After all the components are mounted on the board, the bottom surface of the board is passed through molten lead solder in a wave soldering machine. This machine washes the board with flux to remove contaminants, then heats the board and the components it carries by infrared heat to lessen the possibility of thermal shock. As the underside of the board flows over the completely smooth, thin liquid sheet of molten solder, the solder moves up each wire by capillary action, seals the perforations, and fixes the components in place. The soldered boards are cooled. The PCB is visually inspected at this stage, and imperfect boards are rejected before the encoder mechanism is attached.
The encoder mechanism (including the rubber-covered ball, the support wheel, both spoked wheels and their axles, the LED, and its detector) is assembled as a separate unit. The plastic parts were also manufactured by injection-molding in accordance with proprietary specifications and trimmed of scrap plastic. After the mechanism is assembled, the unit is fastened to the PCB using either clips or screws. The board is now completely assembled and is subjected to an electronics quality control test.
The mouse’s tail—its electrical cable—has also been manufactured using a set of wires, shielding, and the rubber cover. The cable has two additional pieces of molded rubber called overmolds. These are strain relief devices that prevent the cable from detaching from the mouse or its connector plug if the cable is tugged. Mouse makers typically design their own shapes for overmolds. The near-mouse overmold is hooked to the housing, and, at the opposite end of the tail, the connector is soldered to the wires and the connector overmold is popped into place.
The pieces of the outer shell are visually inspected after molding, trimming, and surface (finish) treatment and prior to assembly. The outer shell is assembled in four steps. The completed PCB and encoder assembly is inserted into the bottom of the shell. The buttons are snapped into the top part of the housing, the cable is attached, and the top and bottom are screwed together using automated screwdrivers.
The final electronics and performance quality check is performed when assembly is essentially complete. Rubber
Give your answer to this question below!
What is the easiest and cheapest way to get tooling or moulds made for a short run production?
Question by areena666: What is the easiest and cheapest way to get tooling or moulds made for a short run production?
Our concept design for a new cap closure is nearly finished and we will soon have a few functioning prototypes shortly. However before we go into mass production we feel it will be best to pilot or market test our products to a group of people, our friends and also potential clients.
In order to do this I have been told it may be possible to go to a plastic injection firm and request a short run production..lets say 1000 – 5000 samples
However tooling may be needed….. soft tooling or hard steel tooling..
We are UK based and i have also been advised of not considering China as it is not exactly on our door step if something goes wrong..
Please advise:)
good point..i think i need to rephrase my question…
i have been told nowadays that any form of tooling or moulds can be built but the costs can raise from 1000 up to 100 000……
cheapest – by this i mean cost effective…it is only for samples etc not for mass production
so this for example could be a soft tool, like aluminium,
easiest – i mean by this, maybe there could be a a method I am not aware of…..a simple solution….
Best answer:
Answer by onebear469
why do u think the easiest way would be the cheapist?
What do you think? Answer below!
Q&A: How is a Shampoo Bottle made?
Question by Jenny A: How is a Shampoo Bottle made?
This is for my tech homework. I need to find out how various types of plastic packagings are made and I want to find out how a shampoo bottle is made.
Is it something like vacuum forming, blow moulding or injection holding??
If it is not known how shampoo bottles are made, how are other forms of plastic packagings made??
Does anyone also know if I have have put this in the right category for Yahoo! Answers???
Best answer:
Answer by Coffee cup
Try to check this link, this might help you or give you the idea, at least.
http://www.jobwerx.com/plastics/extrusion.htm
Goodluck!
Add your own answer in the comments!
Home made Injection Mould will not work for me
Hi all, I wanted to see if I could injection mould a cheap little plastic dust pan at home. I was successful in making a concrete mold by using a taped plastic prototype and clay. Turns out that the Smooth-on.com product smooth cast 45 does form the cast, but, it takes way to long to make each piece enough to make any money selling the final pieces. With that in mind, I figured I would try to make a home made injection mould by welding soft iron sheets together. I use the Harbor Frieght sheet metal shears, as well as a chop saw, and they all worked well enough for me to cut the proper sized pieces. The only problem is that the Low Density Poly Ethelyne ( LDPE ) is Way too viscous to flow into any metal form that I make. You will see from the video that even though the melting point of LDPE is 248 F, it does not easily flow into the mould without high presure. If anyone has any suggestion, please feel free to let me know how I can make an injection mold piece at my house.
Video Rating: 4 / 5