Posts Tagged ‘machine’
i wanna know about first injection moulding machine in india?
Question by parmar shashikant r: i wanna know about first injection moulding machine in india?
or hys tory of injection moulidng machine in india plastic injection moulding machine in india
Best answer:
Answer by sr71_usaf
Check this out:
http://www.alibaba.com/countrysearch/IN-suppliers/Moulding_Machine.html
http://www.india-berlin.com/us/e-chronik.htm
What do you think? Answer below!
How much does it cost for an injection mold machine?
Question by frankysnewcolorpainting: How much does it cost for an injection mold machine?
I want to buy an injection mold machine to manufacture my supplies. Whats the most expensive and cheapest machine? Which ones are the best? Whats needed to make my plastic pieces after i buy the machine?
Best answer:
Answer by raven_sunn
http://members.aol.com/skibelt/
http://www.mold-techinc.com/
i hope this helps
What do you think? Answer below!
Tarus Compound Angle Deephole Drilling Machine, Gundrill
Tarus Compound Angle Deephole Drilling Machine, used for Drilling Water Lines and Ejector Pin Holes in Plastic Injection Molds, Die Cast Dies, Compression Molds. Drill/Mill slide tips +/- 15 degrees, worktable rotates infinitely. Rotary table was work-holding magnets embedded into casting by WENN Technologies. Drill, Mil, Tap, Thread on angles. Tarus is located in Sterling Heights, MI USA. We build these machines in other configurations, larger, smaller, without the tip and roatary axes. Other applications include drilling holes for Tube Sheets, Oil Field Equipment and Aerospace Components. www.tarus.com
Video Rating: 5 / 5
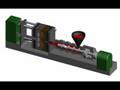
www.custompartnet.com
Video Rating: 4 / 5
machine operation crw d&p
plastic injection machine

Demolding my an address sign for the house, which I cast from aluminum using a simple investment casting technique. See my other video for the pour. The pattern is foam, which is vaporized by molten aluminum, which then fills the cavity. I design plastic housings for a living and so constantly think about the part as it exists in a mold. A lot of effort goes into designing parts that are manufacturable and then chosing gating and mold constructoins that work. Some of that experience has been proving useful in my DIY casting efforts, even though plastic injection tooling is a totally different world. If there’s interest, I’ll keep posting videos of my metal casting experiments.
Video Rating: 5 / 5
SIEMENS S7200 WITH HMI OP 7 FOR INJECTION PLATIC MACHINE

SIEMENS S7200 WITH HMI OP 7 FOR PLASTIC INJECTION MACHINE MODIFIED WITH SIEMENS S7200 AND OP 7 PANEL ZACH FROM AMMAN JORDAN JORDAN FIRST PROGRAM
www.designtekplastics.com Utah based company providing manufacturing of plastic parts, plastic molds, injection mold, injection parts, custom plastic injection molding, to anywhere in the USA
Video Rating: 5 / 5
1999 Battenfeld HM3500-1900 Injection Moulding Machine (1/2)
Call Applied Machinery on 03 9706 8066 for more information on this machine. Used Battenfeld 350 Ton Plastic Injection Moulding Machine, model HM3500-1900. Manufactured in 1999. Features include: – 350 ton clamp pressure – 55mm screw – 2482 bar specific injection pressure – 772ccm theoretical shot volume – 703g shot (PS) – 325mm screw stroke – 1010 x 1010mm platen size – 115mm diameter tie bars – 710 x 710mm between tie bars – 270-690mm min-max mould height – 685mm max opening stroke – 1375mm max daylight – 180mm ejector stroke – Unilog 9000 control – Wetec pick take out robot
Video Rating: 0 / 5
How Does an Injection Moulding Machine Work?
How Does an Injection Moulding Machine Work?
An injection moulding machine is a complex piece of machinery that creates one solid piece by injecting molten materials through a reciprocating screw system into a mould. This machine is made of many components; it is primarily consisted of a hopper, a barrel containing a reciprocating screw, temperature control devices, a clamping unit and the injection mould itself.
The process begins with the creation of a mould. The mould is created by the Toolmakers from the specifications given to them from the designer or engineer via a 3D computer-generated model. The mould is carefully constructed to allow the two halves of the mould — the mould cavity and the mould core — to separate along the parting line. This will allow easy ejection from the injection moulding machine when the part has cooled. If the mould is designed incorrectly the part may catch on the mould, resulting in possible damage.
The specifications and components of the machine must be carefully set up before the process of injection moulding can begin. Temperatures and pressures will be programmed according to the size and shape of the mould and the material that the part is to be made from. Once the machine is set, the cycle will begin and the machine can be left unattended to work its magic.
This is how it works:
Raw material and colour is fed into the barrel of the machine via the hopper. In the barrel the raw materials are subjected to pressure and temperature until they are melted and malleable. The reciprocating screw inside the barrel will turn, injecting a precise amount of the now molten plastic into the injection mould at a set and controlled temperature, pressure and speed. Once the mould is filled with the molten plastic the injection process will shut off. The part is then allowed to cool until it is ready to be taken from the mould. This can take some time depending on the materials, wall thickness, overall size and shape of the part being manufactured. When cool, the mould will open automatically. The mould is inbuilt with an ejecting mechanism which ejects the part in preparation for a new cycle. If a portion of the finished part is still caught in the mould at this point the mould will reopen until the part has been completely ejected. When the part is clear of the machine, the hopper will release more raw material and colour into the barrel and a new cycle will begin. The autonomous nature of the injection moulding machine means it can be left unattended once programmed, and may run continuously throughout day and night.
The basic concept of the plastic moulding machine has been around for over seventy years. Since then the original idea — injecting molten plastic into a mould — has evolved dramatically into an efficient, elegant and versatile tool for creating everyday items.
Dienamics is the only company in Brisbane to offer the complete service of Industrial Design, Toolmaking and Manufacturing. We specialise in the custom moulding of components using engineering thermoplastic resins. For more information, visit <a rel=”nofollow” onclick=”javascript:pageTracker._trackPageview(‘/outgoing/article_exit_link’);” href=”http://www.dienamics.com.au”>Injection Moulding</a>.
Related Plastic Injection Articles
SIEMENS S7 200 AND OP17 DP PLC FOR INJECTION PLASTIC MACHINE 450 TONS
SIEMENS S7 200 AND OP17 DP PLC FOR INJECTION PLASTIC MACHINE 450 TONS FROM ZACH AMMAN JORDAN JORDAN FIRST PROGRAM
Video Rating: 3 / 5
Where could we get an Plastic Extruder Machine and Injection Moulding ?
Question by Pratik P: Where could we get an Plastic Extruder Machine and Injection Moulding ?
Best answer:
Answer by jimbob92065
Probably anywhere in the world exceot for India
What do you think? Answer below!
SIEMENS S7200 AND OP7 PROJECT FOR MACHINE 250 TONS
PLASTIC INJECTION MACHINE 250 TONS MODIFIED WITH S7200 AND HMI OP DP FROM ZACH AMMAN JORDAN JORDAN FIRST PROGRAM
Video Rating: 0 / 5