Posts Tagged ‘Engineering’
Stress Engineering – PET Bottle Stretch-Blow Molding Simulation
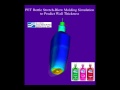
Preform design, blow-molding process conditions, bottle wall thickness distribution and ultimately bottle performance (such as, topload capacity and squeeze/dispensing characteristics) can be optimized using this blow molding simulation coupled with bottle structural analysis. The goal is to minimize the bottle weight and maximize the bottle performance for sustainability. For more information, please visit us at www.stress.com. Contacts us at youtube@stress.com with any questions.
CATIA V6 | Mechanical Engineering & Design | Plastic Part Process
for more info, visit : www.3ds.com Design plastic products and molds with significant productivity gains The plastic part process from design to manufacturing benefits from enhancements in performance and capacity. Embrace a wider scope of complex plastic parts and increase your design efficiency with modeling performances that are enhanced up to 40%, depending on the complexity of the part. In addition, in this dedicated and integrated process, you can choose among an extended library of mold base suppliers, natively incorporating positioning information for standard components. CATIA V6 | Mechanical Engineering & Design | Plastic Part Process
Video Rating: 5 / 5
CATIA V6 | Mechanical Engineering | Bend Part Design | Folded parts from sheetmetal to paper boxes
Expands into manufacturing preparation CATIA V6 strengthens the manufacturing preparation process with Bend Part Design, which enables users to quickly create folded parts across multiple disciplines from sheetmetal to paper boxes. CATIA V6R2011 enriches its mold tooling solution with CATIA Mold Tooling Design product. This specialized application covers the complete tooling process for mold tooling injection designers.
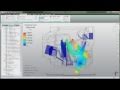
Want more information after viewing this video? Be sure to visit www.autodesk.com and www.SIMSquad.com. Autodesk® Simulation software, part of the Autodesk® solution for Digital Prototyping, provides a range of mechanical simulation tools to help designers, engineers, and analysts make decisions earlier in the engineering design process. With these tools, you can predict the real‐world performance of your product, helping to save the time and money required to build multiple physical prototypes. Autodesk® Simulation software lets you start with mainstream tools and then expand your toolkit to include more advanced simulation such as mechanical event simulation, computational fluid dynamics (CFD), and multiphysics—without the need to learn new workflows. Real-world product behavior is often the result of multiple physical effects interacting simultaneously. With Autodesk® Simulation Multiphysics software, you can study these effects by combining results from different analysis types to help predict a product’s real-world performance. The setup of multiphysics simulations is made easier through the use of standard engineering terminology, workflow guidance, and user-friendly tools and wizards that automate the transfer of simulation results between multiple analyses—letting you focus on product performance, not advanced numerical or simulation methods. Autodesk® Simulation software includes modeling flexibility for multiphysics simulations, allowing you to create meshes …
Scientific Cooling – Burger and Brown Engineering, Inc.
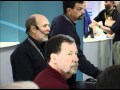
Mark Brown and Philip Burger of Burger & Brown Engineering share there thoughts on the cooling process in injection molding and reveal plans for a training offering.
Video Rating: 0 / 5