Archive for the ‘Video เกี่ยวกับงานฉีดพลาสติก’ Category
madeinchina.com-cixi wanjie electronics co.,ltd
Brief introduction about China suppliers and China products from www.madeinchina.com. This video contains the information of the company that exsists on madeinchina.com– a B2B platform which provides China products and service for worldwide clients. Established in 1992, we are the one of the leading manufacturers and exporters that specializes in terminal blocks, solderless breadboard and electronics-related component for over 15 years. We have a very efficiency management and technical team. During the past years, we have established tooling, plastic injection, moulding plant, hardware process and installation department a series workshop. The rapid development has got through continuous expansion on production equipment, quality improvement and new product line. For better service to our customers, we also accept special requirement for OEM ODM products. According to our accumulated years of experience in marketing, production and development new product, we have confidence to satisfy every need of our customers. We welcome your consideration of our products. Our products are complied with CE, Rohs, UL, and CSA and are certified by ISO9001:2000. Our competitive prices will surely make you possible to penetrate into the market. Established in 1992, the company experience has more than ten years in this field, has set up development of plastic molds, puncher molds, five metals, mold plastics shaping, and a series of departments and workshops for assembling the finished …
Let PT&S Sell your Surplus Equipmpent
With Years of experience PT&S experts have extensive industry-specific networks to connect your equipment to hundreds of international buyers and users of specific equipment types with minimal disruption to your existing process.
Video Rating: 5 / 5
Here’s the venting process for a 2 piece silicone mold. The vents here are simple but the same rules apply to more complicated parts. The mold was made in a previous video using Platsil 73-15. The cast was made using EZ Flo 60 casting resin.
Video Rating: 5 / 5
Loctite MAX2
For the resin transfer molding process, Henkel has developed a new composite matrix resin based on polyurethane which enables improved economics and throughput in processing. Compared to standard epoxy matrix resins, the new Loctite MAX2 cures significantly faster. During injection, it also enables more efficient impregnation without stressing the fibers due to the lower viscosity of the resin.
CATIA V6 | Mechanical Engineering | Bend Part Design | Folded parts from sheetmetal to paper boxes
Expands into manufacturing preparation CATIA V6 strengthens the manufacturing preparation process with Bend Part Design, which enables users to quickly create folded parts across multiple disciplines from sheetmetal to paper boxes. CATIA V6R2011 enriches its mold tooling solution with CATIA Mold Tooling Design product. This specialized application covers the complete tooling process for mold tooling injection designers.
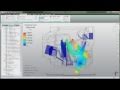
Want more information after viewing this video? Be sure to visit www.autodesk.com and www.SIMSquad.com. Autodesk® Simulation software, part of the Autodesk® solution for Digital Prototyping, provides a range of mechanical simulation tools to help designers, engineers, and analysts make decisions earlier in the engineering design process. With these tools, you can predict the real‐world performance of your product, helping to save the time and money required to build multiple physical prototypes. Autodesk® Simulation software lets you start with mainstream tools and then expand your toolkit to include more advanced simulation such as mechanical event simulation, computational fluid dynamics (CFD), and multiphysics—without the need to learn new workflows. Real-world product behavior is often the result of multiple physical effects interacting simultaneously. With Autodesk® Simulation Multiphysics software, you can study these effects by combining results from different analysis types to help predict a product’s real-world performance. The setup of multiphysics simulations is made easier through the use of standard engineering terminology, workflow guidance, and user-friendly tools and wizards that automate the transfer of simulation results between multiple analyses—letting you focus on product performance, not advanced numerical or simulation methods. Autodesk® Simulation software includes modeling flexibility for multiphysics simulations, allowing you to create meshes …
RJ BILLET ALUMINUM Powder Coated CLOCK CNC Milled WITH YOUR NAME CUSTOM MADE USA 8
Do you needUSA extreme machining cnc machine work or USA aluminum zinc brass Molding or USA Plastic injection molding or USA water jetting done on a project? We have simplified this process so anyone can get it done. Please visit our web site for more information & products. www.vendio.com To receive a 5% discount please tell them the Shark sent you. In addition, tell them were you saw the add at. Like YOUTUBE. Come down & visit us at H&S Machine 3403 South 1400 West Suite B West Valley City, Utah, 84119-4050 Phone Gregg 801-755-7627 machine shop foreman PLEASE LEAVE A NAME & # WE DO NOT ALWAYS GET TO THE PHONE IN TIME. We are open MS 9 am to 7 pm mountain time. Send all questions & prints to hsmachinegregg@gmail.com If you need parts made in the USA by real professionals PLEASE INCLUDE YOUR 411 info… NAME & YOUR PHONE # IN ALL CORRESPONDENCE. WE CANNOT CONDUCT BUSINESS WITH YOU WITH OUT IT! MENTION WHERE YOU SAW THIS ADD & RECEIVE A 5% DISCOUNT WHEN YOU STOP BY OUR PLACE OF BUSINESS.
Video Rating: 3 / 5
Video Rating: 5 / 5
DIY Plastic Parts

I’ve got one word for you. “Plastics” Yes, it’s what whales and seals are having for lunch.
Video Rating: 4 / 5
There is an updated video of this, now WITH AUDIO!!! Here is a quick fly through of how to make a plastic injection mold by using Solidworks. First you can see that I am making a simple solid, make sure that it has ample draft. The radii are un important but aids in presentation. Second I am shelling the object to a suitable thickness, remember with plastics a consistent wall thickness is key! I then make a sketch that will define the limits of the mold itself. Next I am defining the parting line, this is the line that Solidworks uses to define the separation of the mold cavity and core sides. I am also turning on draft analysis to help show me that my object is of suitable geometry to part. After that, you cant see it, but I check for shut-off surfaces; I have none. Then by selecting the parting lines I can then create a parting surface, this is the surface that the mold cavity will shut off against when closed. Once those steps are completed I can define my tooling slip, I choose interlock and the approximate thicknesses of each mold half. From there I move each half apart to reveal a mold! When all the steps have been done save the cavity and core sides into seperate files. Next CORES, SLIDES, AND LIFTERS!
Video Rating: 1 / 5
JMB PROCESS ON ROBOT
robot i processed and set up on a cincenati injection molding press… interesting right … lol it is!!!
Video Rating: 5 / 5
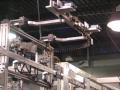
Plast06 Exhibition
Formech exhibiting at the Plast06 in Milan in partnership with Autotype, Camattini and Abacus to promote and link the vacuum forming and IMD process, as well as to create complete CAD and tooling solutions. Formore information on the machines in this video, or any others in our product range please visit out website: www.formech.com Alternatively, please feel free to contact us via our facebook page if you have any enquiries: www.facebook.com You can also stay up to date by following us on twitter: twitter.com
Video Rating: 4 / 5
Low Volume Metal Components – Low Volume Plastic Components – Armstrong
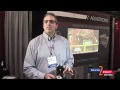
Armstrong Mold Corporation is another preferred supplier found at www.D2P.com. Need Low Volume Metal Components or Low Volume Plastic Components, look to Armstrong. Our company manufactures metal and plastic components in prototype and low-volume production quantities. Whether it is 1 or 5000 parts, we deliver production-grade components and assemblies that meet your demanding delivery schedules. With our manufacturing process, we can assist you in producing everything from prototype die castings to large plastic enclosures. Rubber Plaster Molding (RPM) Graphite Die Casting Precision Airset Sand Casting One-Shot Casting Reaction Injection Molding (RIM) Rapid Injection Molding via Cast Tooling CNC Machining and Hogouts Find this company and others at http
Prosin Molds designed and built a 2 colour mold for a system that runs in a conventional molding machine. Introduced at the NPE show in Chicago, the system ran flawlessly for the entire week. The system featured: A 10 cavity, 2 colour mold. In mold action to separate the materials. Injection timed bonding of the materials. Mold mounted injection unit for the secondary material. Fused Cooling Technology: Superior consistency for better part quality. Accesses difficult areas to decrease cycle time. Minimizes pressure drop, reducing energy demands on process services.
Sustainable Spoons.flv
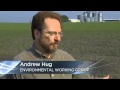
Nearly 40 billion plastic utensils are used in the US alone, per year. These utensils are made from hard plastic that will take thousands of years to decompose in a landfill but Seymour, Indiana-based Cereplast may have just the solution. Cereplast Inc. designs and manufactures proprietary bio-based, renewable plastics which are used as substitutes for petroleum-based plastics in all major converting processes–such as injection molding, thermoforming, blow molding and extrusions. Bioplastics begins with the extraction of sugars and starches from plants like corn, tapioca and potatoes. The sugars are then either fermented or converted into a biopolymer, which is the basic building block of bioplastics. Frederic Scheer, CEO of Cereplast, further explains the process of this great discovery.
Video Rating: 5 / 5
KUKA robots work alongside RAS MULTIBEND-CENTER in state-of-the-art production line. MULTIBEND-CENTER is the name of the bending center from RAS Reinhardt Maschinenbau GmbH for flexible sheet-metal working. In a state-of-the-art production line, two KUKA robots load and unload this bending system. The customer required a system concept that could be integrated smoothly into the existing production system.
Video Rating: 4 / 5