Archive for the ‘Video เกี่ยวกับงานฉีดพลาสติก’ Category
射出成形金型ができるまで 〜放電加工〜
プラスチック射出成形金型の設計、製造、メンテナンスを行っている「株式会社ムトウ」 が射出成形金型ができるまでのプロセスをムービーで紹介します。 Phase4は、放電加工です。放電加工は絶縁状態の油中で、対象物と放電マスターと呼ばれる電極を接近させて放電させます。この行程では、マシニングセンタで切削加工された金型部品にエッジ形状を追加しています。 The process for injection mold. Phase 4 – Electrical Discharge Machining
Video Rating: 5 / 5
Static Stress, Linear Dynamics, and Heat Transfer Overview – Autodesk Simulation
Want more information after viewing this video? Be sure to visit www.autodesk.com and www.SIMSquad.com. Autodesk® Simulation software, part of the Autodesk® solution for Digital Prototyping, provides a range of mechanical simulation tools to help designers, engineers, and analysts make decisions earlier in the engineering design process. With these tools, you can predict the real‐world performance of your product, helping to save the time and money required to build multiple physical prototypes. Autodesk® Simulation Mechanical and Autodesk® Simulation Multiphysics software includes tools for static stress and linear dynamic simulations—helping you study stress, strain, displacement, shear, and axial forces resulting from structural loading—including forces, moments, pressures, gravity, and displacements. Autodesk® Simulation software also helps you determine a part’s natural frequencies and mode shapes in order to avoid frequencies that are disruptive or harmful to your design. In addition, it helps you avoid structural failure by determining the amount of load that would cause a structure to buckle—letting you review the predicted buckling shape so you can then add supports and stiffeners to your design. Autodesk® Simulation software includes support for steady-state and transient heat transfer simulations—helping to predict changes in a product’s temperature profile in order to reveal potential failure. Study linear and nonlinear thermal effects by considering …
Video Rating: 5 / 5
MachiningMold.mov
This mold was used to injection mold a plastic part for the Harbortronics VGD70 vertical grip, for the Nikon D70. Quite the process… I learned about injection molding, made my own manual molding machine, learned about CNC machining, and eventually CNC’d a manual mill from harbor freight. In the end, it was all worth it… we made many hundreds of the grips, and they were well liked by customers!
Video Rating: 0 / 5
Bihler INLINE-FERTIGUNG
www.bihlernc.de Fertigungstechnologien intelligent kombinieren Neue Wege zur Herstellung von Hybrid-Baugruppen Steigende Variantenvielfalt und immer kleinere Serien verlangen flexibelste Fertigungssysteme. Die Bihler-Systemtechnik bietet im Bereich der Herstellung von Hybridbauteilen intelligente Lösungsansätze: sie kombiniert die Stärken unterschiedlichster Fertigungs-Technologien auf einer Produktionsanlage. Das Fallbeispiel präsentiert die vollautomatisierte Inline-Fertigung einer variablen Schalterbaugruppe auf dem NC-Fertigungs- und Montagesystem BIMERIC BM – ausgehend vom Rohband über NC-Stanz-, Biege-, Schweiß-, Gewinde- und Montageprozesse inkl. Kunststoffumspritzprozess zum einbaufertigen Produkt. Combining production technologies intelligently New ways to produce hybrid assemblies Increasing variety and ever smaller production series demand highly flexible production systems. Bihler’s system technology offers intelligent solutions in the field of hybrid parts, by combining the strengths of extremely varied production technologies in one production system. The result is fluid, highly flexible inline processes for made-to-measure products with maximum product quality. The case example presents the fully automated inline production of a variable switch assembly on the NC production and assembly system BIMERIC BM – starting with the blank metal strip and including NC stamping, bending, welding, thread forming, assembly processes and the plastic injection moulding …
double injection
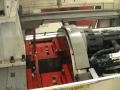
Double Shot injection or 2K moulding is referring to injection 2 material at the same time. This technique will help to save some assembly jobs. www.gf-technology.com
Top Teh production cell awarded with Step in to the future award Shown products: 1. Sumitomo (SHI) Demag Intelect 100 fully electrict direct drive injection molding machine fitted with activeLock and activeFlowbalance to have the highest precision and repeatability with lowest possible energy consumption 2. Wemo 8-5 cartesian robot with Eco Mode – fastest cycle with lowest energy consumption. A robot with the easiest programming interface 3. Plastic Systems DWC 75 – dry air dryer that monitors material consumption and adjust drying parameters accordingly. Best process with up to 3x less energy than standard twin tower molecular sieve dryers. 4. Save materbatch consumption with MGF gravimetric feeder. You can reach return of your investment within 6 months! 5. Frigel RAD 80 – high precision micro chiller with high flow capability. The item displayed was running 100% faster than under standard condition using standard cooling equipment – simply impressive! The displayed production production cell has shown huge production cost saving potential while increasing quality of the product.
Video Rating: 0 / 5
Injection Molding Lesson 4
Injection Molding Lesson 4
Video Rating: 0 / 5
ambientedirect.com: Kartell – Thalya
The Thalya chair by Patrick Jouin for Kartell fascinates with its simple shape and detail loving texture. The transparent and coloured polycarbonate chair is decorated on seat and back rest using the process of injection moulding. This special manufacturing process creates vertical and horizontal lines. The lines are soft, rounded and accomplish an almost “feminine” shape.
Video Rating: 3 / 5
Khatod Coating Technologies
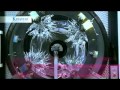
Khatod Optoelectronic Srl – High Tecnology, Best Quality Service: This Is Our Must Khatod is the unique company on the international scene that specifies and develops the entire product process 100% in-house. Since 1985, Khatod has held all of its operations in its headquarter (Milano, Italy) a full optical service – from project to object – encompassing optical and mechanical designs, mould fabrication, injection moulding, test and inspection, as well as the time to market, are under our full control. Our quality starts from close collaboration with selected suppliers, world leaders in plastic materials, control instruments, and machines for polymers transformation process. Most of the technologies used to produce our millions of parts per month, are created by our team of engineers who develop our new, technically unique products as well as creating the necessary tooling and equipment to manufacture them. Today, we are proud to announce that, since the beginning of 2012 Khatod has equipped its Production Department with the most advanced vacuum treatment plant based on the latest cutting-edge VACUUM COATING TECHNOLOGIES, specific for coating our Optical Reflector Systems for LED applications. Always in the same spirit: 100% in-house, under our full control, from project to object, our aim is to deliver our customers the highest quality level. The realization of our vacuum treatment plant has been carried out in collaboration with the R&D of one of the most important …
Auslegung von Temperierkanälen mit Künstlicher Intelligenz (KI)
Kunststoffverarbeitende Prozesse wie das Spritzgießen benötigen stabile und homogene Werkzeugtemperaturverteilungen, um wirtschaftlich und schnell eine gute Produktqualität zu erreichen. Die Integration konturnaher Temperierkanäle wurde in den letzten Jahren durch die Entwicklung neuer Werkstoffe und Herstellungsverfahren ermöglicht. Dadurch stieg jedoch der Aufwand für die manuelle Auslegung von geeigneten Temperierkreisläufen. Mittels Algorithmen der Künstlichen Intelligenz und naturanaloger Verfahren können Temperiersysteme neuerdings automatisiert ausgelegt werden. Weitere Informationen zum Projekt “NeuroTemp” unter www.neurotemp.iph-hannover.de. Design of temperature control systems by using artificial intelligence (AI) Plastic processing processes like the injection moulding need stable and homogeneous temperature distribution, in order to reach a good product quality fast and economically. The integration of temperature control systems near to the part contour was made possible in the last years by the development of new materials and manufacturing processes. Thus however the time and effort for the manual lay out design of suitable temperature control systems rose. By using algorithms of artificial intelligence and nature-similar procedures temperature control systems can be designed recently automated.
Penne Company Presentation
High-tech solutions for metal and plastic parts of the highest quality. That is what our company has specialised in for over 30 years. We are involved in every step of the process: you tell us what part you need and we’ll develop and manufacture the necessary dies and injection moulds — and of course the part itself. In other words, we take over complete responsibility, from design to mass production. A simple component of a kitchen implement or a high-tech car part? We will meet your most diverse requirements, from design to production. Are you already one of our customers? Then you know that we are always striving for excellence. If you are not yet one of our customers, we invite you to get to know us. We believe in long-lasting business relationships and do everything we can to become your preferred supplier.
Video Rating: 5 / 5